Top Materials Used in Medical Sheet Metal Fabrication - A Comprehensive Guide
Medical sheet metal fabrication is a critical process in the healthcare industry. It involves the creation of precise, durable components for medical devices and equipment.
The choice of material plays a pivotal role in this process. It directly impacts the performance, safety, and longevity of the final product.
This comprehensive guide aims to shed light on the top materials used in medical sheet metal fabrication. We'll delve into the properties, applications, and benefits of each material.
We'll also guide you on how to choose the right material for your specific needs. This includes considering factors like application requirements, regulatory compliance, and cost-effectiveness.
Furthermore, we'll discuss the importance of precision in fabrication and the role of certifications. We'll also explore why HLH is a preferred choice for medical sheet metal fabrication.
Whether you're a manufacturing startup founder, a robotics engineer, or a medical device designer, this guide is designed to equip you with the knowledge you need to make informed decisions in your fabrication projects.
Understanding Medical Sheet Metal Fabrication
Medical sheet metal fabrication involves crafting metal components specifically for medical use. This process is crucial in creating parts for medical devices that require high precision and safety. The quality and precision demanded in the medical field make it distinct from other types of metal fabrication.
The process starts with selecting the appropriate medical-grade materials. These materials must adhere to strict safety and performance standards. Next, advanced manufacturing techniques like laser cutting and CNC machining shape these materials into precise components.
Precision is non-negotiable in medical fabrication. The use of advanced technologies ensures that parts meet exact specifications. Even the smallest variations can have significant impacts, potentially affecting patient safety.
Commonly used materials include:
· Stainless Steel
· Titanium
· Aluminum
· Copper Alloys
Each material offers unique properties, catering to different needs and applications. The final choice depends heavily on the specific use and regulatory requirements of the device or equipment in question.
Understanding the intricacies of medical sheet metal fabrication is essential for anyone involved in the production of medical devices. From startup founders to seasoned engineers, familiarity with these processes ensures better product development and faster time to market.
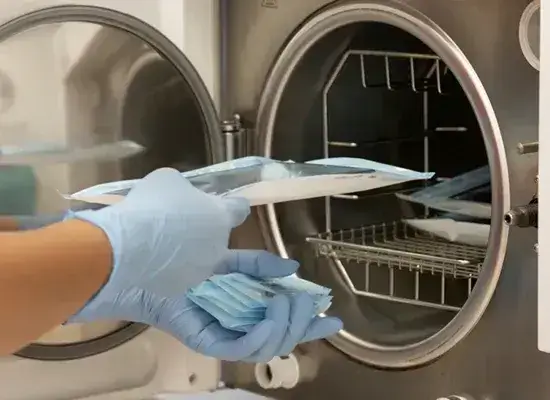
Key Materials in Medical Sheet Metal Fabrication
In the realm of medical sheet metal fabrication, choosing the right materials is crucial. Each material serves unique functions and is selected based on application demands. Understanding the properties of these materials is foundational for precise fabrication.
Medical-grade materials must meet strict standards for safety and efficacy. Stainless steel, titanium, aluminum, and copper alloys are popular choices. These materials are favored for their specific benefits in different medical environments.
Stainless Steel: The Go-To Choice
Stainless steel stands out for its durability and corrosion resistance. In medical settings, these qualities are essential. Moreover, it is easily sterilized, making it ideal for surgical tools and equipment.
Its strength ensures longevity, reducing the need for frequent replacements. The material is also versatile, suitable for a wide range of medical applications. This versatility explains why it's a staple in medical fabrication projects.
Titanium: Strength and Biocompatibility
Titanium is renowned for its strength and lightweight properties. This combination is crucial for implants and prosthetics. It offers unmatched biocompatibility, minimizing the risk of allergic reactions within the body.
Its use extends beyond implants to support structures that require both strength and minimal weight. Titanium’s unique properties make it a preferred choice for many medical devices, delivering durability without added bulk.
Aluminum: Lightweight and Durable
Aluminum is chosen for its excellent strength-to-weight ratio. This makes it ideal for portable medical devices and equipment. Its lightness does not compromise durability, ensuring reliability in demanding environments.
The material is also cost-effective, contributing to lower manufacturing costs. Its ease of manufacturing allows for rapid prototyping, which is critical in iterative design processes. These factors make aluminum a pragmatic choice in medical fabrication.
Copper Alloys: Antimicrobial Properties
Copper alloys offer valuable antimicrobial properties, crucial in preventing infection. Surfaces and devices made from copper alloys can reduce pathogen transmission. This makes them suitable for high-touch areas in medical facilities.
While less commonly used than other materials, copper alloys are vital in applications where hygiene is paramount. Their ability to continuously kill bacteria complements the stringent hygiene standards required in medical settings.
How to Choose the Right Material for Your Application
Selecting the appropriate material for medical sheet metal fabrication is essential for success. Each project's demands can vary, influencing material choice. The goal is to match material properties with application needs.
Start by evaluating the end-use of the fabricated part. Consider environmental conditions it will face, such as exposure to chemicals or moisture. Durability and strength are key factors, especially for devices under constant strain.
Compliance with industry regulations is non-negotiable. Materials must meet specific standards for safety and efficacy. This ensures that the final product is safe for use in medical settings.
Cost is another critical consideration. High-quality materials might elevate initial expenses, but can reduce long-term costs through durability. Lightweight options can contribute to easier handling and transport.
When selecting a material, it's vital to:
· Evaluate mechanical properties and performance requirements
· Consider environmental exposure and risks
· Assess cost implications and lifecycle
· Ensure compliance with regulatory standards
Ultimately, the right material will offer a balance of performance, safety, and cost-effectiveness, tailored to the specific needs of your project.
Choose the Right Material for Your Application
Talk to our experts. Our qualified engineers are always happy to answer your questions.
Considering the Application and Regulatory Compliance
A material's suitability often hinges on its application context. Assess the part's function and environment. For instance, implants demand biocompatibility, while surgical tools need high corrosion resistance.
Regulatory compliance is paramount. FDA and ISO standards ensure medical-grade quality. Adhering to these standards secures product safety and market entry.
Integrating compliance and application insights into decision-making fosters successful material selection. This approach aligns product performance with regulatory demands, ensuring a seamless development process.
The Role of Certifications in Material Selection
Certifications play a crucial role in material selection. They verify that materials meet industry standards. For medical applications, standards like ISO 13485 are pivotal.
Such certifications confirm a manufacturer’s adherence to quality protocols. They guarantee that materials consistently meet medical safety requirements. This consistency is essential for maintaining trust with end-users.
When choosing materials, ensure your supplier holds relevant certifications. This assures quality and compliance, safeguarding the integrity of your medical products.
Why HLH Sheet Metal for Medical Sheet Metal Fabrication

When it comes to medical sheet metal fabrication, HLH Sheet Metal stands as a leader. Our dedication to precision and quality sets them apart. The company’s expertise spans various medical applications.
We offers cutting-edge technology and skilled craftsmanship. These ensure the creation of components with exacting standards. The results are reliable and consistent medical devices.
Our well-rounded approach considers every aspect, from design to production. This seamless integration speeds up the development process. It effectively reduces time-to-market for medical devices.
Moreover, HLH Sheet Metal is known for its adaptability. The company accommodate diverse project needs and stringent specifications. This flexibility is essential for meeting dynamic industry demands.
Trusting HLH Sheet Metal means investing in quality and precision. The company's reputation in the industry is unparalleled. When you need reliable fabrication, HLH Sheet Metal is the name to know.
Precision Metal Fabrication with HLH Sheet Metal
Precision is the cornerstone of our fabrication process. We employ advanced technologies like CNC machining and laser cutting. These methods ensure every part meets stringent tolerances.
We prioritizes attention to detail at every step. This dedication to precision enhances product quality significantly. Each component is crafted to exact specifications.
Collaborating with HLH Sheet Metal guarantees high-fidelity parts. The precision of metal fabrication process is unmatched. It results in components that perform reliably in critical applications.
HLH Sheet Metal's Commitment to Quality and Certifications
Quality assurance is integral to our operations. The company uphold strict standards across all phases of production. This commitment begins from the initial design to the final inspection.
Holding certifications like ISO 13485 showcases our dedication to compliance. These certifications reinforce the company's reliability in the medical field. HLH ensure products meet all necessary regulatory requirements.
By choosing HLH Sheet Metal, you benefit from a partner who prioritizes quality. Our certified processes guarantee top-tier medical components. This focus ensures every project adheres to global standards.
Choosing a Trusted Medical Metal Equipment Manufacturer
Selecting the right manufacturer is crucial for medical device success. Trust and reliability cannot be compromised. This decision impacts both production quality and timeline adherence.
Start by evaluating the manufacturer’s track record. Experience in medical metal fabrication assures competency. Proven expertise is key to navigating complex requirements.
Certifications and compliance are non-negotiable elements. They indicate the manufacturer's adherence to medical standards. Ensuring this can prevent costly regulatory setbacks.
Consider the technological capabilities offered by the manufacturer. Advanced tools often equate to higher precision and efficiency. Superior technology contributes to better quality outputs.
Finally, assess the manufacturer’s communication and support. Clear communication ensures smooth project progression. A responsive team can tackle challenges promptly.
Experience and Quality Control
Experience equips a manufacturer with invaluable insights. Experienced manufacturers foresee and mitigate potential risks. Their historical knowledge strengthens the fabrication process.
Quality control systems are pivotal in maintaining product standards. Rigorous checks reduce defects and enhance reliability. Consistent quality inspections are hallmarks of trustworthy manufacturers.
Not all manufacturers are equal in quality assurance. Choose those who emphasize stringent quality control. Their commitment to excellence solidifies their credibility.
The Importance of a Seamless Supply Chain
A seamless supply chain underpins punctual delivery. Efficient logistics ensure components arrive on schedule. This continuity is essential to prevent production delays.
Reliability in sourcing materials is equally vital. Manufacturers with strong supplier relations ensure steady material flow. This minimizes disruptions and maintains production momentum.
Furthermore, transparency within the supply chain builds trust. Knowing each stage helps predict potential issues early. Thus, enabling preemptive measures to tackle supply chain challenges.
Conclusion: Ensuring Success in Medical Metal Fabrication
Success in medical metal fabrication hinges on informed decisions and strategic partnerships. Selecting the right materials based on application and compliance is fundamental. Each choice impacts both device functionality and regulatory approval.
Equally crucial is choosing a manufacturer with a solid reputation. Experience and quality control ensure precision and reliability in production. This choice is pivotal for meeting stringent medical standards.
Finally, effective communication and a streamlined supply chain complement these efforts. Together, these elements lay the groundwork for efficient and successful medical metal fabrication. Informed choices today lead to a robust and compliant product tomorrow.
Choose the Right Material for Your Application
Talk to our experts. Our qualified engineers are always happy to answer your questions.