Table Of Contents:
- ISO Standards for Metal Parts Manufacturing: Comprehensive Guide to Certification, Compliance, and Benefits
- What Are ISO Standards and Why Are They Crucial for Metal Parts Manufacturing?
- How Does ISO 9001 Certification Impact Metal Parts Manufacturing Quality?
- What Is ISO 3834 and How Does It Ensure Welding Quality in Metal Fabrication?
- Which Metal Fabrication Processes Must Comply With ISO Standards?
- How Do ISO Standards Benefit Specific Industries in Metal Parts Manufacturing?
- What Are the Practical Steps and Checklists for ISO Compliance in Metal Parts Manufacturing?
- What Are the Overall Benefits of ISO Certification for Metal Parts Manufacturing Companies?
- What Are Common Questions About ISO Standards for Metal Parts Manufacturing?
- Final Thoughts
ISO Standards for Metal Parts Manufacturing: Comprehensive Guide to Certification, Compliance, and Benefits
Metal parts manufacturing is a technical field where precision, quality, and consistency are paramount. This guide explains how ISO standards ensure that manufacturing processes meet rigorous quality benchmarks while streamlining operations and boosting customer satisfaction. Whether you are an engineer, product designer, or procurement manager, understanding ISO standards can enhance your quality management systems, internal audits, and overall market reputation. Here, we cover how certifications such as ISO 9001 and ISO 3834 impact manufacturing quality, welding services, and process compliance, while offering practical checklists, training resources, and cost-reduction benefits for organizations.
Let’s begin our in-depth journey into the world of ISO standards and the advantages they bring to metal parts manufacturing companies.
What Are ISO Standards and Why Are They Crucial for Metal Parts Manufacturing?
ISO standards are internationally recognized benchmarks defining minimum quality, safety, and efficiency levels for products and processes. In metal fabrication, they set uniform criteria for testing, inspection, and certification of parts manufactured for industries such as aerospace, automotive, and construction. By providing a common language, ISO standards ensure customers receive products that meet predetermined performance specifications.
Adherence to these standards helps manufacturers decrease waste, eliminate defects, and streamline production. Moreover, compliance with ISO standards improves market access by enhancing reputations among international partners and stakeholders, reduces incidents of product recalls, minimizes hazards, and supports internal audits for efficient supply chain operations. This standardization further improves communication with suppliers and strengthens stakeholder collaboration for long-term business sustainability.
How Does ISO 9001 Certification Impact Metal Parts Manufacturing Quality?
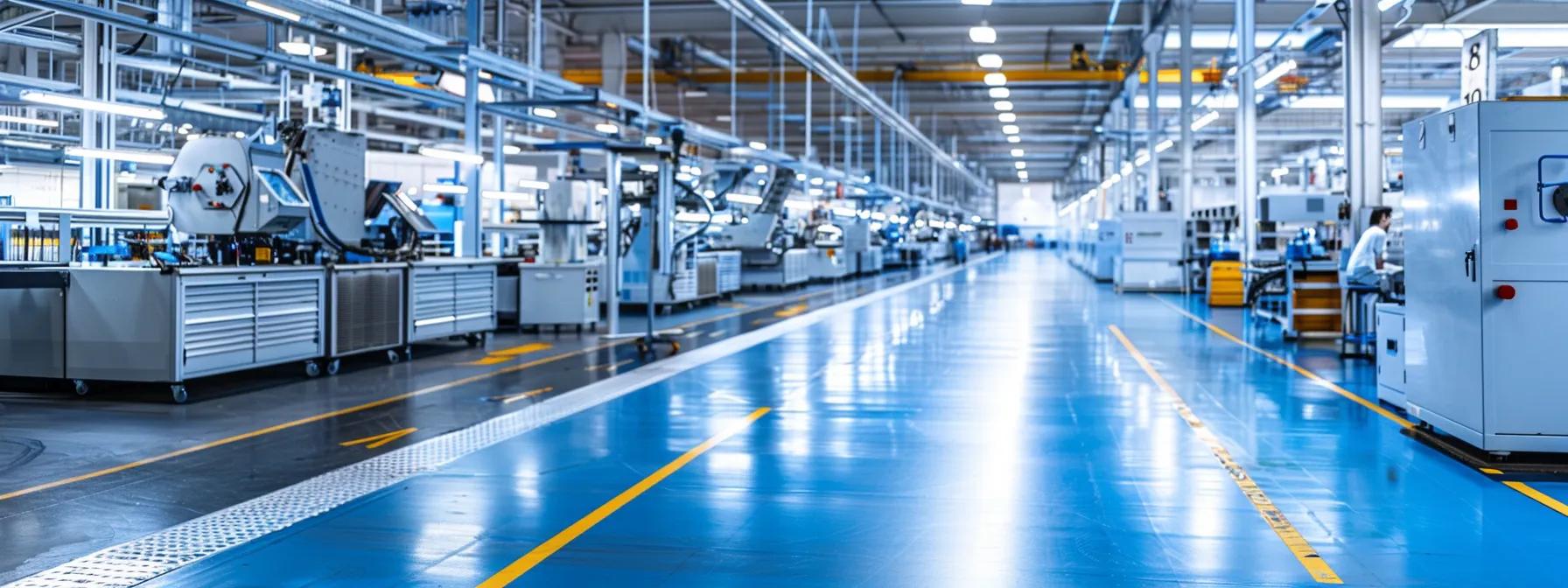
ISO 9001 certification impacts quality management and operational efficiency by setting specific requirements for quality management systems. Its systematic approach to quality assurance encourages continuous measurement, analysis, and process improvement.
What Are the Key Requirements of ISO 9001 for Metal Parts Fabricators?
ISO 9001 requires metal parts fabricators to establish robust documentation, process controls, and regular performance audits.
Critical procedures include:
- Inspecting incoming materials
- In-process evaluations
- Final quality control tests
Clear documentation for tracking and tracing products is mandatory, along with corrective actions and regular internal audits. These requirements reduce process variability and ensure every product leaving the production line meets high-quality standards.
Read More About How To Choose A Metal Parts Fabricator From China
What Benefits Does ISO 9001 Bring to Metal Parts Manufacturing Companies?
Benefits include enhanced customer satisfaction through consistent quality, improved operational efficiency by reducing waste, and a strengthened market reputation. Additionally, it opens up new revenue streams by increasing customer trust and reduces risks associated with product failures and recalls, thus saving costs and resources.
How Can Metal Parts Manufacturers Achieve ISO 9001 Certification?
The certification process begins with a gap analysis comparing existing quality systems against ISO requirements. Manufacturers then develop comprehensive process documentation, train staff on ISO procedures, and conduct internal audits to identify improvement areas. External certification bodies perform unbiased audits to confirm compliance, and ongoing internal audits and corrective actions ensure continued performance optimization and innovation.
What Are Common Challenges in Maintaining ISO 9001 Compliance?
Challenges include evolving industry standards, workforce turnover, and integrating new technologies. Maintaining up-to-date documentation and consistent internal audits can be resource-intensive. However, regular training, updated quality control software, and proactive risk management help overcome these challenges, resulting in a resilient and efficient manufacturing operation.
Looking For ISO Certified Metal Parts Manufacturer From China
Talk to our experts. Our qualified engineers are always happy to answer your questions.
What Is ISO 3834 and How Does It Ensure Welding Quality in Metal Fabrication?
ISO 3834 provides detailed requirements for personnel, equipment, and process qualifications specifically for welding operations. In metal fabrication, where welding is central, this standard guarantees that welded joints are strong, durable, and safe.
What Are the Certification Steps for ISO 3834 in Welding Services?
Welding service providers start by reviewing and documenting their welding procedures and work environment. They ensure that welders are trained and equipment meets necessary specifications. An independent certification body then audits these processes. Once any gaps are addressed, certification is awarded, with regular follow-up audits to maintain high welding quality.
How Does ISO 3834 Certification Benefit Welding Operations?
Benefits include consistent weld quality, reduced rework rates, and improved process efficiency. Certification instills customer confidence and helps secure contracts, particularly in sectors with strict quality requirements like aerospace, automotive, and construction. Moreover, ISO 3834 provides a framework for continuous learning and improvement in welding practices.
How Does ISO 3834 Complement Other ISO Standards in Metal Parts Manufacturing?
ISO 3834 complements ISO 9001 by focusing specifically on welding—a critical subprocess. Together, they ensure that both the overall production system and the welding operations adhere to stringent quality criteria, thereby minimizing production risks and enhancing product reliability.
Which Metal Fabrication Processes Must Comply With ISO Standards?
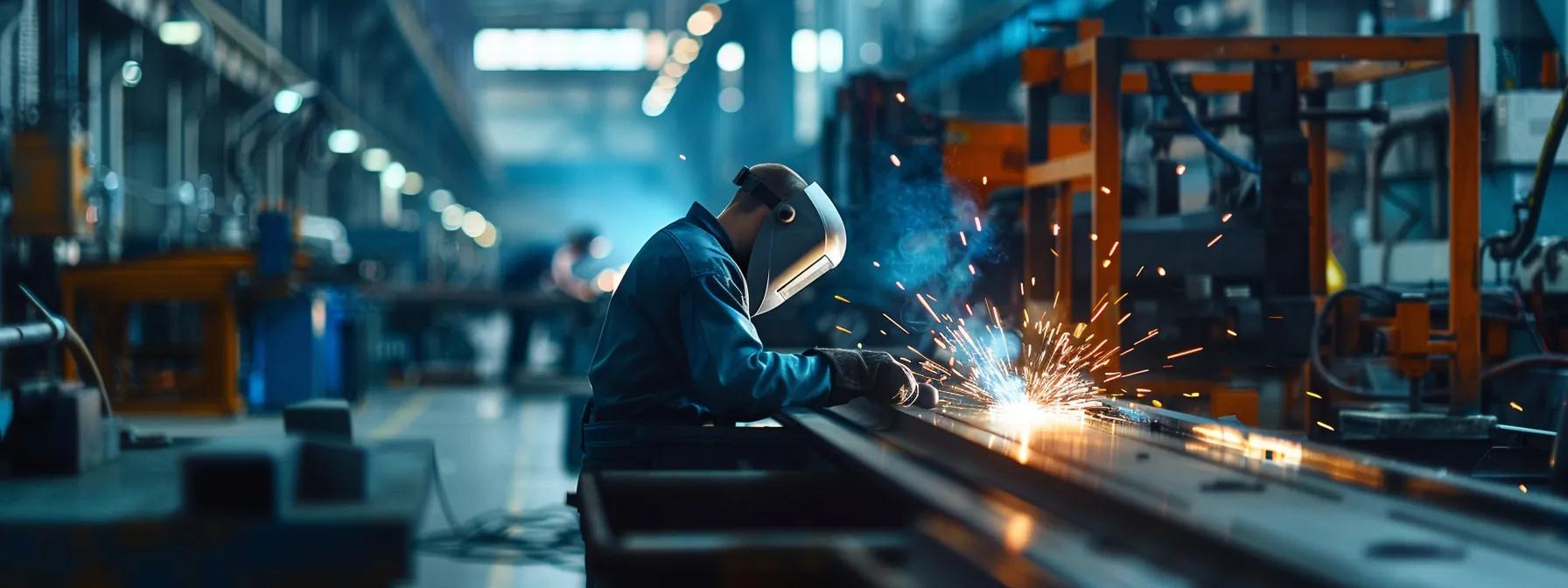
ISO compliance governs every stage of production, from design to finishing, ensuring high-quality benchmarks in processes such as welding, metal cutting, and finishing. Each process benefits from specific ISO requirements which maintain quality consistency, optimize techniques, minimize defects, and reduce variability.
How Are Precision Welding Services Certified to ISO Standards?
Precision welding services achieve certification by implementing rigorous quality management processes. This involves documenting welding procedures, training personnel, using advanced equipment, and performing regular internal audits. External certification audits further confirm that the welding practices meet international standards.
What Are the ISO Requirements for Metal Cutting Services?
ISO requirements for metal cutting focus on precision, tolerance, and surface finish. Manufacturers must regularly calibrate cutting equipment and maintain documentation of processes and quality inspections to guarantee that components meet strict dimensional tolerances and surface standards.
How Does Metal Finishing Meet ISO Quality and Compliance Criteria?
Metal finishing processes like polishing, painting, and plating are critical for durability and aesthetic appeal. ISO criteria emphasize uniform surface quality, corrosion resistance, and adhesion. Manufacturers must adhere to performance criteria and conduct regular tests in controlled environments, ensuring finished products meet stringent standards.
ALSO READ: How To Choose The Right Custom Metal Fabricator
How Do ISO Standards Benefit Specific Industries in Metal Parts Manufacturing?
Different industries benefit uniquely from ISO standards. Aerospace, automotive, and construction sectors demand exceptional precision and reliability. ISO certification enables companies to address industry-specific requirements, mitigate operational hazards, manage resources efficiently, and enhance safety protocols, thereby securing a strong market presence.
What Are the ISO Compliance Requirements for Aerospace Metal Fabrication?
Aerospace metal fabrication requires extreme reliability. Manufacturers must document every production step, routinely calibrate equipment, and maintain traceability records. Strict adherence to regulatory and safety benchmarks minimizes risks of in-flight malfunctions and ensures components meet the highest quality levels.
How Does ISO Certification Enhance Automotive Metal Parts Manufacturing?
In automotive manufacturing, part durability, crash safety, and environmental compliance are critical. ISO certification guides design decisions by emphasizing robust materials and production processes. It helps manufacturers meet legal and customer requirements, build trust with OEMs, and reduce recall risks through improved quality control.
Why Is ISO Certification Important for Construction Metal Fabrication?
For construction, ISO standards ensure that metal parts are structurally robust and can withstand harsh environmental conditions. Certification covers key factors such as stress, load distribution, corrosion resistance, and proper finishing. This reduces risks of collapse or degradation, protecting both lives and property while enhancing business stability for contractors and suppliers.
What Are the Practical Steps and Checklists for ISO Compliance in Metal Parts Manufacturing?
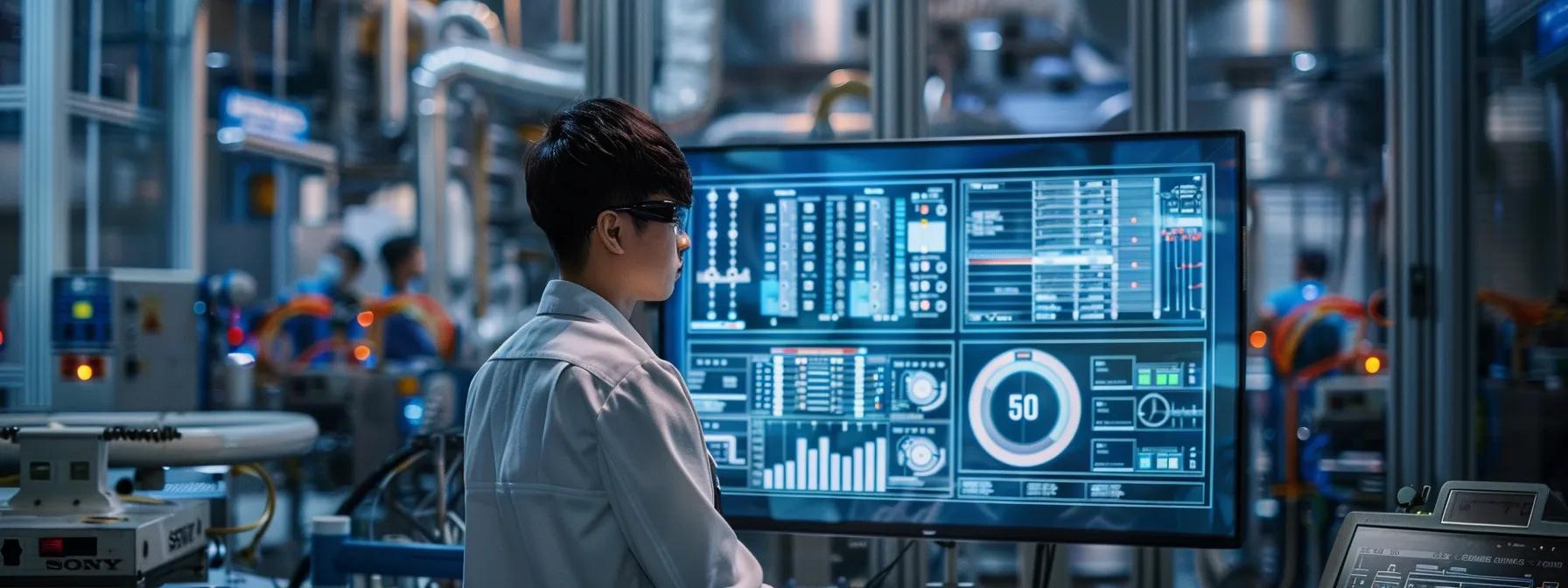
Achieving ISO compliance requires thorough planning, regular internal audits, and robust employee training. A comprehensive compliance checklist covering every stage—from design to final inspection—is essential for aligning processes with ISO standards. Practical steps include conducting risk assessments, developing detailed process documentation, and scheduling frequent reviews to identify improvement areas.
What Is Included in an ISO Compliance Checklist for Metal Parts Manufacturers?
A typical checklist includes:
- Documentation of processes
- Equipment calibration records
- Employee training logs
- Quality control procedures
It often covers raw material inspection, tracking process deviations, corrective and preventative actions, and regular review meetings. This structured checklist not only simplifies certification but also serves as a benchmark for continuous quality improvement.
How Can Metal Parts Manufacturers Prepare for ISO Certification Audits?
Manufacturers should start with an in-depth internal audit using the compliance checklist. This process identifies areas requiring improvement ahead of the external audit. Comprehensive employee training, updated documentation, and mock audits further ensure readiness. Engaging an external consultant can provide an unbiased perspective to smooth the certification process.
What Training Is Available for ISO Standards in the Metal Fabrication Industry?
Training programs and certification courses are available in various formats—workshops, online courses, and in-person sessions. These programs focus on quality management, process optimization, documentation practices, and audit readiness, equipping teams with the skills needed to maintain compliance and foster a culture of continuous improvement.
What Are the Overall Benefits of ISO Certification for Metal Parts Manufacturing Companies?
ISO certification offers multiple benefits including a framework for continuous quality improvement, enhanced customer confidence, waste reduction, and minimized production errors. Certified organizations enjoy fewer defects, cost savings, and improved operational efficiency. Moreover, ISO certification serves as a market differentiator, facilitating business expansion and providing a competitive edge globally by strengthening reputation and optimizing supply chain management.
How Does ISO Certification Improve Quality Control and Customer Satisfaction?
By enforcing rigorous testing, documentation, and review processes, ISO certification ensures that every component meets strict quality benchmarks. This systematic approach reduces defects, fosters customer trust, and enables quick resolution of issues, ultimately boosting customer satisfaction.
In What Ways Does ISO Certification Reduce Costs and Increase Efficiency?
Standardized processes and continuous improvement methods help reduce resource wastage and minimize errors. Early detection of inefficiencies through internal audits allows for prompt corrective actions, reducing downtime and material loss. Streamlined supply chain coordination further cuts costs, making operations leaner and more competitive.
How Does ISO Certification Provide a Competitive Advantage in the Metal Fabrication Industry?
ISO certification demonstrates a company’s unwavering commitment to quality, reliability, and continuous improvement. Clients in sectors such as aerospace, automotive, and construction prefer ISO-certified manufacturers for the assurance of high-quality products and adherence to safety standards. This reputation boosts market access, helps win new contracts, and supports long-term client relationships in a fiercely competitive global market.
What Are Common Questions About ISO Standards for Metal Parts Manufacturing?
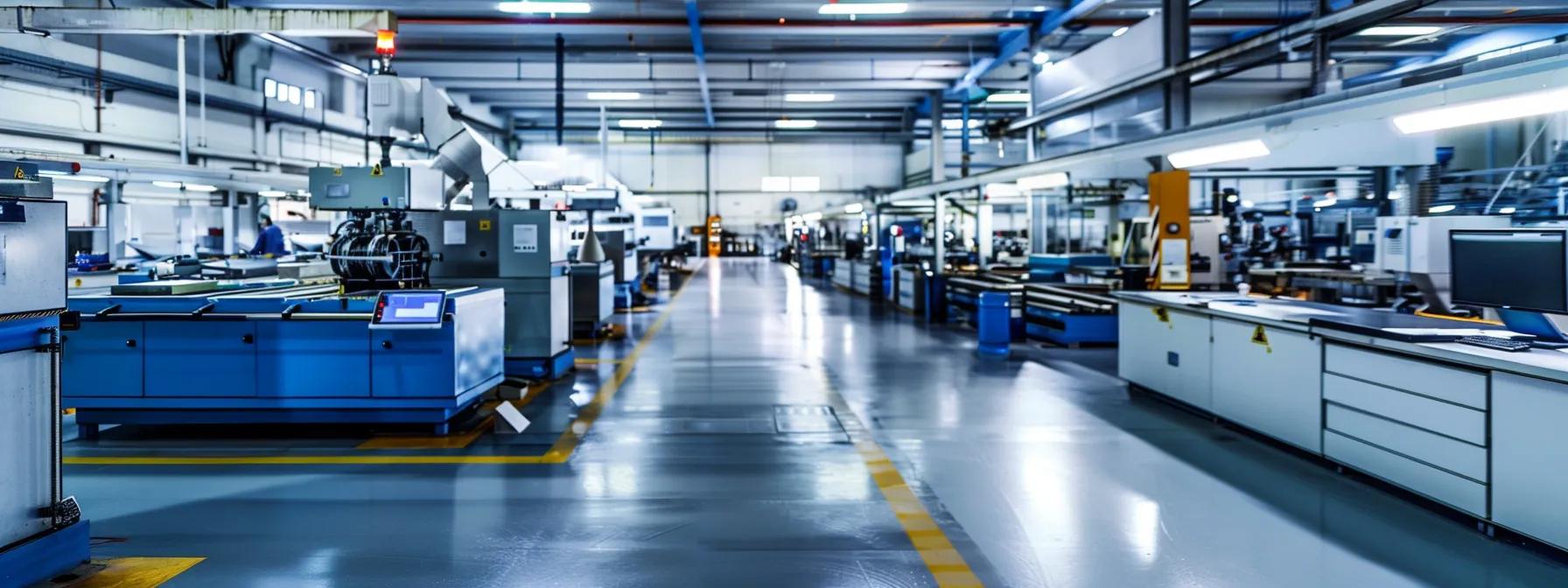
FAQs
What Is the Difference Between ISO 9001 and ISO 3834?
ISO 9001 addresses overall quality management systems and the consistency of product quality, while ISO 3834 focuses on welding processes to ensure high-quality welded joints. The former covers broad production practices; the latter targets critical welding operations.
How Long Does It Take to Get ISO Certified in Metal Parts Manufacturing?
The certification process in metal parts manufacturing generally takes between six months and a year, depending on the complexity of existing quality management systems, documentation readiness, and the number of production lines.
Can Small Metal Fabricators Benefit From ISO Certification?
Absolutely. Small fabricators can improve process reliability, reduce risks, and enhance brand reputation. Increased market access and customer trust can spur growth even on a limited scale.
How Often Must ISO Certifications Be Renewed or Audited?
ISO certifications are typically valid for three years, with annual surveillance audits required to ensure continued compliance. Regular audits help incorporate continuous improvements into processes.
What Processes Should Metal Parts Manufacturers Prioritize for ISO Compliance?
High-impact processes such as welding, metal cutting, and finishing should be prioritized since they directly affect product quality and customer satisfaction. Implementing ISO standards in these areas ensures key performance specifications are met.
What Role Does Documentation Play in Maintaining ISO Standards?
Documentation forms the backbone of the quality management system. Comprehensive process maps, quality control records, and audit reports ensure transparency, facilitate internal audits, and meet certification requirements.
How Can ISO Certification Improve Supply Chain and Internal Collaboration?
By standardizing procedures, ISO certification enhances communication across the production process, creating a synchronized supply chain. Regular audits and standardized documentation improve resource planning and reduce risks, thereby boosting overall efficiency.
Why Are ISO Standards Critical for Metal Parts Manufacturing?
ISO standards ensure that manufacturing processes meet global quality and safety benchmarks. They provide a framework for consistent quality control, enhance process reliability, and reduce defects, leading to cost savings and improved customer satisfaction.
How Does ISO 9001 Certification Impact Operational Efficiency?
By enforcing systematic quality management practices, ISO 9001 helps streamline production processes, reduce waste, and quickly identify inefficiencies. This results in cost savings, enhanced efficiency, and a stronger market reputation.
What Are The Main Challenges of Maintaining ISO Certification?
Challenges include managing evolving standards, keeping documentation current, and training personnel. However, strategic internal audits and corrective actions help overcome these issues, leading to improved quality management.
How Does ISO 3834 Enhance Welding Quality in Metal Fabrication?
ISO 3834 sets clear, precise requirements for welding processes, ensuring that personnel, equipment, and procedures meet high standards. This reduces defects and complements the overall quality assurance achieved through ISO 9001.
What Steps Are Necessary to Prepare for an ISO Certification Audit?
Preparation involves conducting an internal review using a compliance checklist, updating documentation, training staff, and performing mock audits. An external consultant can help ensure readiness and a smooth audit process.
How Do ISO Standards Affect Supply Chain Management in Metal Parts Manufacturing?
ISO standards standardize processes and establish clear performance benchmarks, enhancing transparency and supplier collaboration while reducing risks and ensuring consistent quality across all components.
Final Thoughts
ISO certification is vital for metal parts manufacturing companies aiming to maintain high quality, efficiency, and competitiveness. By implementing robust systems such as ISO 9001 and specialized standards like ISO 3834, manufacturers can reduce defects, streamline processes, and enhance market reputation. These certifications deliver significant cost savings, improved operational transparency, and greater customer satisfaction. Embrace ISO standards to secure a competitive edge and elevate your manufacturing practices to meet global benchmarks.
Process | ISO Standard | Key Requirement | Benefit | Measurement |
---|
General Quality | ISO 9001 | Documented quality management | Enhanced reliability | Audit score |
Welding | ISO 3834 | Qualified personnel and controlled procedures | Improved weld integrity | Defect rate |
Metal Cutting | ISO 9001 | Precision calibration and maintenance | Reduced dimensional variance | Tolerance level |
Metal Finishing | ISO 9001 | Uniform surface treatment | Consistent aesthetic quality | Surface finish |
Documentation | All ISO | Comprehensive record keeping | Enhanced traceability | Process logs |
Before integrating ISO standards, use a compliance checklist to verify every process from raw material inspection to final product testing meets required benchmarks. This table summarizes core aspects essential for ISO compliance while outlining measurable benefits that impact production, quality, and overall efficiency.
Leveraging ISO certifications not only secures compliance with international quality benchmarks but also fosters a culture of continuous improvement. The resulting advantages include stronger customer relationships, improved market access, and a competitive edge in the fast-evolving field of metal parts manufacturing. Adopt these practices diligently to achieve operational excellence and sustainable business success.
Looking For ISO Certified Metal Parts Manufacturer From China
Talk to our experts. Our qualified engineers are always happy to answer your questions.