Table Of Contents:
- CNC Machining Techniques for Unmatched Precision
- What Are the Key CNC Machining Techniques for Precision Manufacturing?
- Which Materials Are Best Suited for Precision CNC Machining?
- How Do CNC Machining Techniques Meet Industry-Specific Precision Requirements?
- What Are the Advantages of CNC Machining for Achieving Unmatched Precision?
- How Can You Optimize CNC Machining Processes for Maximum Precision?
- What Are the Latest Trends and Technological Advances in Precision CNC Machining?
- How Can You Choose the Right CNC Machining Service for Unmatched Precision?
- Frequently Asked Questions
- Final Thoughts
CNC Machining Techniques for Unmatched Precision
Precision manufacturing delivers high-quality parts with tight tolerances and consistent performance. In today’s competitive marketplace, producing components that meet exact geometric requirements and functional specifications is essential. Whether you work with metals like titanium and stainless steel or intricate plastics and composites, CNC machining techniques have become indispensable for aerospace, automotive, medical, and robotics industries. This article discusses the key CNC machining techniques that deliver unmatched precision, the best-suited materials, how these techniques overcome industry-specific challenges, and strategies to optimize your machining workflow for maximum accuracy.
The analysis below provides a series of technical questions answered with precision and supported by illustrative examples. This resource links each technique to its benefits and applications while showing how these advanced methods drive productivity, reduce waste, and ensure repeatability.
What Are the Key CNC Machining Techniques for Precision Manufacturing?
CNC machining techniques are the backbone of precision manufacturing, enabling high accuracy with various materials and complex geometries. Key techniques include milling, turning, multi-axis machining, Swiss machining, and EDM, each offering refined and repeatable results.
How Does CNC Milling Achieve High Precision?
CNC milling uses computer-controlled rotary cutting tools to remove material from a workpiece with exact positioning commands from the program. Milling machines are built with rigid structures and advanced controllers that resist vibrations and optimize cutting parameters via adaptive control software. For instance, in aerospace applications, aluminum components can be milled with tolerances as tight as ±0.005 inches. Multi-tool setups also reduce repositioning errors and enhance overall dimensional accuracy. This technique is widely used in automotive and medical device manufacturing, supporting automation for high-volume production.
What Makes CNC Turning Essential for Accurate Part Production?
CNC turning produces symmetric parts by rotating the workpiece against a stationary cutting tool. This process is ideal for creating cylindrical shapes with high repeatability and minimal deviation from design. Advanced control systems adjust speeds and feed rates to maintain consistent accuracy; for example, stainless steel shafts can achieve surface finishes of Ra 0.8 with concentricity tolerances within 0.002 inches. With capabilities for both roughing and finishing in one cycle, CNC turning is efficient, reduces scrap, and is critical for rotational components in turbine engines and medical devices.
How Does Multi-Axis CNC Machining Enhance Complex Geometry?
Multi-axis CNC machining allows the simultaneous control of four, five, or more axes, enabling the cutting of intricate curves, angles, and contours that are impossible with traditional 3-axis machines. This technique minimizes setups by allowing multiple approaches to the workpiece, reducing errors and saving time. Aerospace components with curved surfaces and internal features benefit from tolerances within ±0.003 inches. Automated tool path planning and collision avoidance further enhance precision and efficiency, making multi-axis machining popular for both prototyping and small-batch production.
Why Is Swiss CNC Machining Ideal for Small, Intricate Parts?
Swiss CNC machining is optimized for producing small, delicate parts requiring extreme precision and consistency. The workpiece is supported very close to the cutting tool by a guide bushing, minimizing deflection and vibration. This setup achieves tolerances as low as ±0.001 inches and is ideal for medical implants, watch components, and micro-mechanical assemblies. Automated bar feeding and the ability to perform multiple operations in one setup further reduce errors and improve throughput, making it indispensable in high-volume precision applications.
How Does CNC EDM Provide Precision for Hard Materials?
Electrical Discharge Machining (EDM) provides precision for machining hard or difficult-to-machine materials such as tool steels, titanium alloys, and superalloys. CNC EDM operates by generating controlled electrical sparks between the workpiece and an electrode to erode material with high accuracy. It is capable of creating complex cavities and profiles with tolerances better than ±0.002 inches. Precise control over electrical discharge parameters ensures repeatability and excellent surface integrity with minimal thermal damage, making EDM ideal for high-precision dies and molds in aerospace and automotive applications.
Which Materials Are Best Suited for Precision CNC Machining?
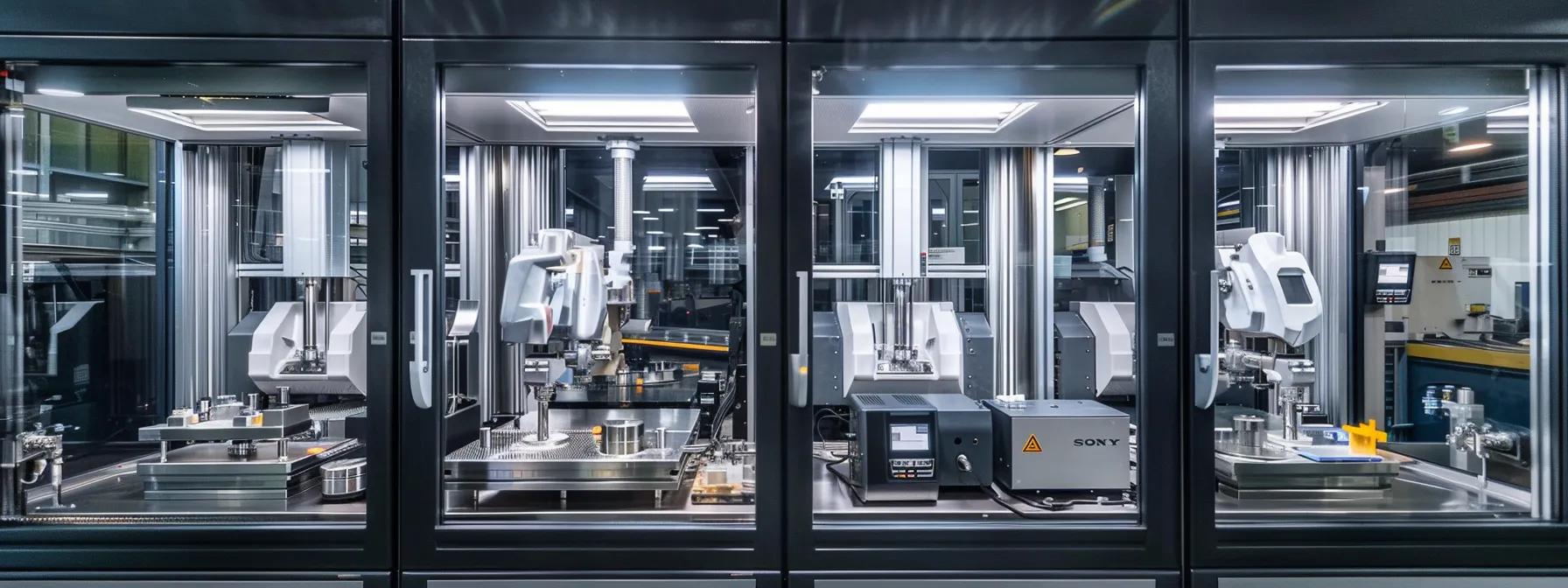
Choosing the right material is crucial for performance and durability in CNC machined parts. Materials offer different strengths, machinability, and thermal resistance. Here, we review aluminum, stainless steel, titanium, plastics, and composites for precision machining.
ALSO READ: Advanced Materials in Sheet Metal Fabrication
What Are the Advantages of Aluminum in CNC Machining?
Aluminum is popular for its lightweight strength, high thermal conductivity, and excellent machinability, which allow rapid cutting speeds and long tool life. Aluminum parts can achieve surface finishes below Ra 1.6 microns and tolerances within ±0.005 inches. Its corrosion resistance and non-magnetic properties make it suitable for high-performance aerospace and automotive applications. Additionally, aluminum’s ductility enables machining of intricate geometries without cracking or warping, making it ideal for both prototypes and mass production.
How Does Stainless Steel Support Tight Tolerances in CNC Processes?
Stainless steel is valued for exceptional strength, durability, and corrosion resistance. It can maintain tight tolerances even under high-stress conditions. Machining processes can achieve tolerances as fine as ±0.003 inches, ensuring that components fit precisely in assemblies. Although stainless steel requires specialized tools and techniques due to its work-hardening nature, modern CNC equipment and advanced cutting fluids mitigate these challenges. This makes stainless steel essential for medical devices and industrial machinery where both strength and precision are required.
Why Is Titanium Preferred for High-Precision CNC Parts?
Titanium is prized for its excellent strength-to-weight ratio, biocompatibility, and corrosion resistance. It is the material of choice in aerospace, medical implants, and high-performance sporting goods. Although more challenging to machine, advancements in cutting tools have enabled titanium parts with tolerances within ±0.004 inches. Its ability to withstand high temperatures and stresses makes it indispensable where failure is not an option. Specialized coatings on cutting tools further improve machining consistency and surface finish, ensuring both durability and precision.
What Role Do Plastics and Composites Play in CNC Machining?
Plastics and composites are critical for applications requiring lightweight structures, electrical insulation, or customized properties. Materials such as nylon, polyoxymethylene (POM), and polyether ether ketone (PEEK) offer excellent machinability and achieve tolerances comparable to metals. These materials are used in consumer electronics, automotive components, and industrial applications where chemical resistance and performance are key. Composites, combining fibers with polymer matrices, provide enhanced strength-to-weight ratios and resilience under stress, and they allow for quick prototyping and low-volume production with high precision.
How Do CNC Machining Techniques Meet Industry-Specific Precision Requirements?
Each industry imposes unique standards, and CNC machining is tailored to meet these stringent requirements for reliability and performance in various applications.
What Precision Challenges Does Aerospace CNC Machining Address?
Aerospace applications manufacturing require extreme precision due to safety-critical operating conditions. CNC machining in aerospace must achieve tolerances around ±0.003 inches to ensure aerodynamic performance and structural integrity. Complex geometries like turbine blades and fuselage components are produced using multi-axis machines and advanced cooling systems that reduce thermal expansion. Real-time monitoring and adaptive controls further ensure that challenging materials such as titanium and high-strength aluminum alloys are machined to exact standards.
Related Article: Overcome Your Precision Metal Fabrication Challenges Today
How Is CNC Machining Used for Medical Device Manufacturing?
Medical device manufacturing demands high precision along with biocompatibility and sterility. CNC machining produces surgical instruments, implantable devices, and diagnostic equipment with tolerances below ±0.002 inches. Processes are designed to machine both metals and polymers safely for human use. For example, titanium implants benefit from precise machining that ensures excellent strength and biocompatibility, while Swiss CNC machining is often employed for extremely small, intricate components. Rigorous quality control ensures all parts meet strict regulatory standards.
Why Is Automotive CNC Machining Critical for Performance Parts?
Automotive components must balance performance, safety, and cost-effectiveness. Engines, transmissions, and suspension systems are CNC machined with tolerances around ±0.004 inches to ensure efficient performance under dynamic loads and thermal stress. Techniques like multi-axis machining and laser-assisted cutting are used to machine complex engine blocks and critical components, contributing to overall safety and performance. Rapid prototyping further helps automotive manufacturers accelerate development cycles and reduce time-to-market.
How Does CNC Machining Support Consumer Electronics Precision?
Consumer electronics require miniaturized components with extremely tight tolerances, often as low as ±0.001 inches. CNC machining is used to produce housings, connectors, and circuit components from materials like aluminum and high-performance plastics. Advanced spindle technologies and precise tool path programming ensure that even small production runs meet the exacting standards of quality and efficiency demanded in this fast-paced industry.
What Are the Advantages of CNC Machining for Achieving Unmatched Precision?
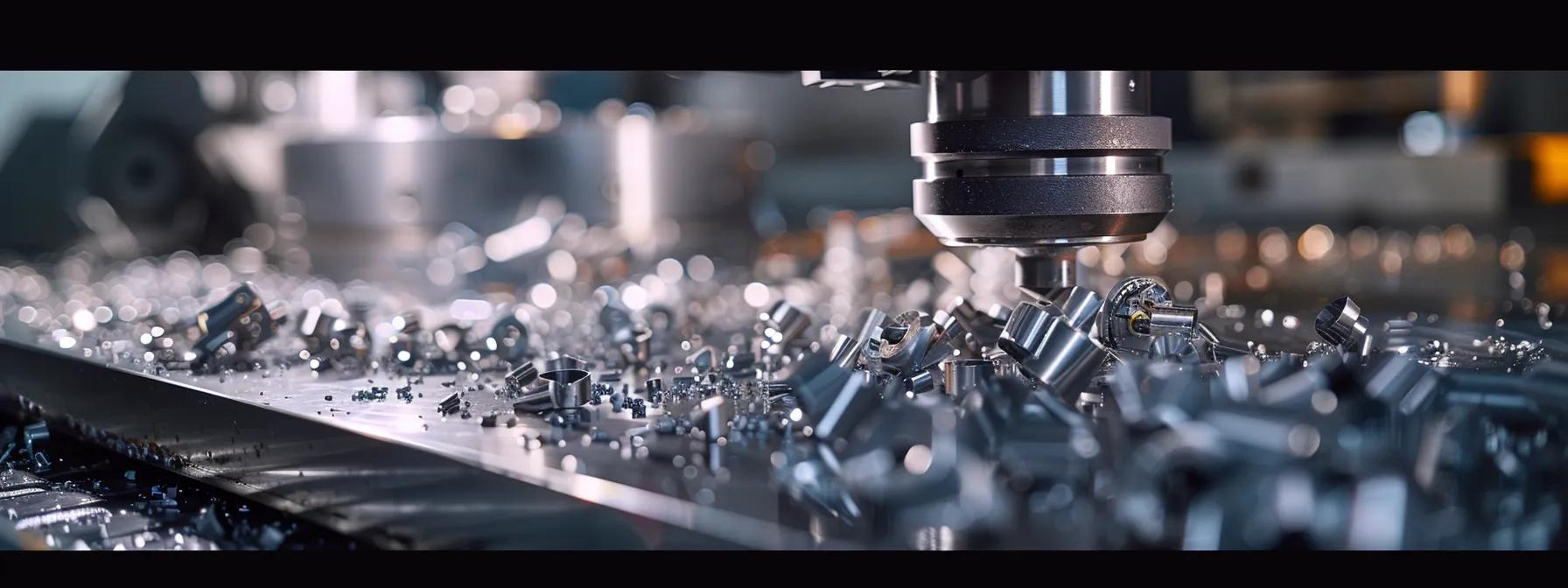
CNC machining provides several advantages that translate into unmatched product precision, including tight tolerances, repeatability, and rapid prototyping capabilities.
How Do Tight Tolerances Improve Product Quality?
Tight tolerances ensure that each component meets its specifications and functions properly within an assembly. Deviations as small as ±0.002 to ±0.005 inches reduce the need for rework and adjustment, directly impacting product quality. In fields like aerospace and medical devices, such precision is closely linked to performance and safety, resulting in fewer failures and enhanced customer satisfaction.
What Role Does Advanced Equipment Play in Precision?
State-of-the-art CNC machines with high-speed spindles, rapid tool changers, and real-time monitoring systems are essential for achieving superior precision. Advanced software controllers and adaptive feedback loops further optimize each cut, ensuring minimal tool wear and vibration. Features such as collision detection and automatic error correction improve production reliability and reduce downtime, making advanced equipment critical in the pursuit of stringent tolerances.
How Does Engineering Support Enhance CNC Machining Accuracy?
Expert engineering support is crucial throughout the CNC process, from design to final inspection. Engineers refine CAD/CAM programs, select suitable cutting tools, and adjust machining parameters to fit specific materials and design requirements. Rigorous quality control measures, including statistical process control and precision measurement using CMMs or laser scanners, ensure that parts consistently meet the desired tolerances while minimizing waste.
Why Is Rapid Prototyping Important for Precision Manufacturing?
Rapid prototyping allows for quick validation of designs and machining processes before full-scale production. By producing highly accurate prototype parts that simulate the final product, manufacturers can test, refine, and ensure that every component performs under real-world conditions. This iterative process reduces development cycles, accelerates time-to-market, and leads to improvements in product quality and manufacturing efficiency.
Save Manufacturing Costs With Advanced Techniques
Talk to our experts. Our qualified engineers are always happy to answer your questions.
How Can You Optimize CNC Machining Processes for Maximum Precision?
Optimizing CNC machining processes is crucial for both precision and efficiency. This involves refining design guidelines, material selection, and workpiece preparation to achieve consistent results.
What Are Best Practices for CNC Machining Design Guidelines?
Effective design guidelines begin with creating parts that feature uniform wall thickness, minimized sharp corners, and properly sized fillets and chamfers. Designing for manufacturability—considering machine capabilities and optimal tool paths—reduces the possibility of errors and rework. Simulation software and virtual machining allow for the prediction of potential issues, ensuring that CAD models are tailored for efficient machining.
How Do Material Selection and Preparation Affect Precision?
The properties of different materials, such as hardness, thermal conductivity, and ductility, directly influence machining performance. For example, titanium and stainless steel may require slower feeds and specialized tools compared to aluminum. Additionally, proper material preparation—including stress relieving, fixturing, and surface conditioning—ensures that the workpiece maintains accurate dimensions throughout the machining process, leading to consistently precise parts.
What Are Common CNC Machining Tolerances and How Are They Achieved?
Common tolerances in high-precision industries vary from ±0.001 inches for critical components to ±0.005 inches for less demanding parts. Achieving these tolerances involves compensating for factors like thermal expansion, tool deflection, and machine rigidity. High-precision instruments such as CMMs and laser scanners are used to continuously monitor dimensions, with adjustments made in real time via the CNC controller.
How Does Multi-Axis Machining Improve Precision on Complex Parts?
Using additional axes allows the machine to access the workpiece from multiple angles, reducing the need for repeated setups and minimizing cumulative errors. This constant tool engagement helps capture intricate details and results in superior surface finishes and dimensional accuracy. The combined use of advanced controllers and predictive software enables real-time adjustments that enhance production efficiency.
What Are the Latest Trends and Technological Advances in Precision CNC Machining?
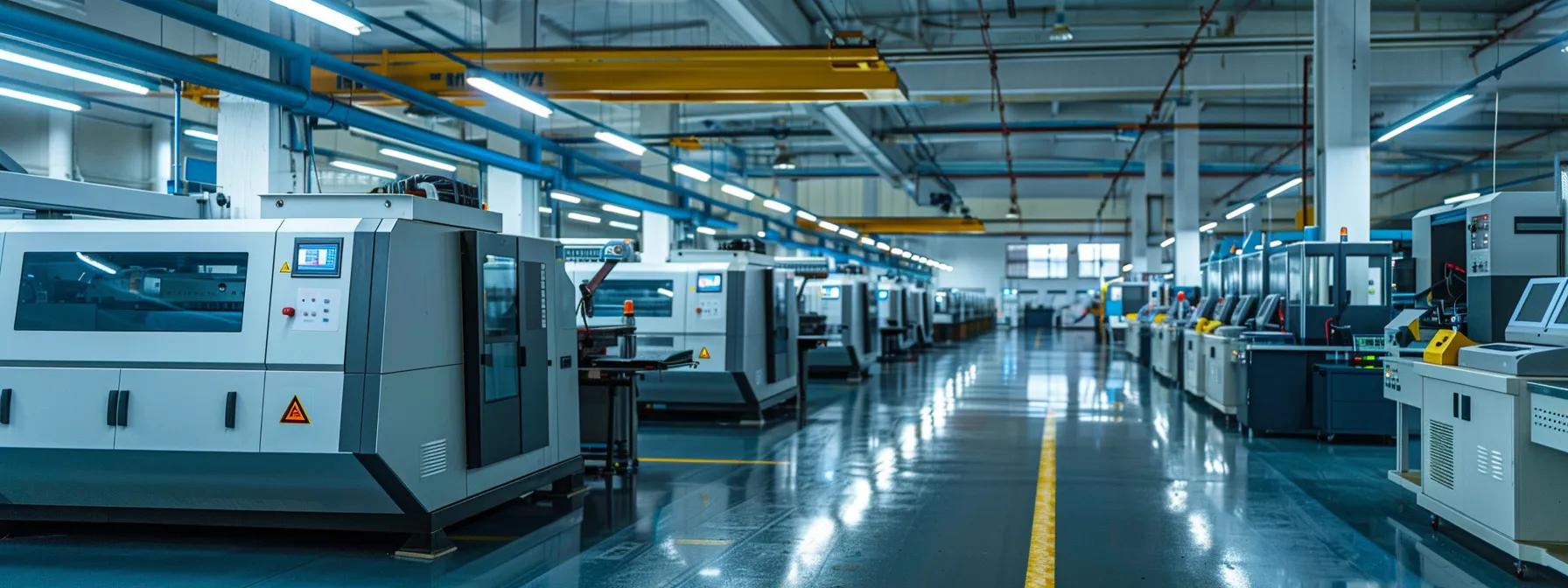
CNC machining technology continues to evolve. Trends such as increased automation, deeper software integration, the introduction of new materials, and sustainability practices are driving greater precision and efficiency.
How Is Automation Enhancing CNC Machining Precision?
Automation reduces human error by employing robotic systems, automated tool changers, and real-time monitoring. These systems maintain consistent machining conditions and enable continuous production with minimal downtime. Integrated sensor feedback allows for instantaneous adjustments, resulting in improved accuracy and lower scrap rates, which is essential for high-volume manufacturing.
What Are the Impacts of Software Integration on CNC Accuracy?
Advanced CAD/CAM software facilitates detailed modeling, simulation of tool paths, and the early detection of potential issues. Combined with real-time monitoring systems, this integration allows manufacturers to adjust machining parameters dynamically, greatly reducing variability and ensuring each part conforms closely to design specifications.
How Are New Materials Influencing Precision Machining?
Emerging materials, including high-performance polymers, advanced composites, and novel metal alloys, expand the capabilities of CNC machining. These materials present unique challenges that have spurred improvements in cutting tools and machining strategies. Innovations driven by these material demands ensure that precision and productivity are maintained even as new applications emerge.
What Sustainability Practices Support Precision Manufacturing?
Sustainable CNC machining focuses on reducing waste by optimizing tool paths and lowering machining times. Energy-efficient machinery and renewable energy sources, along with recycling of machining chips and environmentally friendly cutting fluids, help reduce the overall environmental impact while maintaining high precision. These practices not only meet regulatory standards but can also lower production costs.
ALSO READ: Precision Machining Services Deliver Exceptional Metal Parts
How Can You Choose the Right CNC Machining Service for Unmatched Precision?
Selecting a CNC machining service is a vital decision that influences product quality and manufacturing efficiency. Key factors to consider include precision capabilities, quality control measures, and a proven track record supported by case studies.
What Should You Look for in a Precision CNC Machining Provider?
Evaluate the provider’s experience with high-precision projects and verify certifications relevant to your industry, whether aerospace, medical, or automotive. Check the range of materials handled and the machining processes available (multi-axis, Swiss, EDM, etc.). Ensure that the provider employs robust quality control processes and has documented case studies or customer testimonials attesting to their ability to meet required tolerances. Additionally, factor in lead times, transparent pricing, and reliable customer support.
How Do Case Studies Demonstrate Precision Capabilities?
Case studies offer tangible evidence of a provider’s ability to handle complex geometries and strict tolerances. They detail how projects were executed—such as machining titanium components within ±0.003 inches using multi-axis systems—and illustrate the provider’s commitment to quality and continuous improvement. Reviewing these examples helps to gauge a provider’s technical expertise and reliability.
What Questions Should You Ask About CNC Machining Tolerances?
Inquire about the typical tolerance ranges the provider can consistently achieve for different materials and machining processes. Ask about their process control methods and what post-machining inspection techniques (such as CMM or laser scanning) are used to validate final dimensions. Understanding these aspects will help determine if the provider can meet the precision standards required for your projects.
How Does Pricing Relate to Precision and Quality?
Pricing should reflect the level of precision and quality delivered. While competitive pricing is important, lower costs might indicate compromises in machine maintenance, tooling, or quality control. Ensure that the custom metal parts price is transparent and accounts for setup, prototyping, and quality inspections. A quality-focused provider will be able to justify their pricing with proven success and certifications.
Frequently Asked Questions
Q: What factors are most critical when choosing a CNC machining service?
A: Critical factors include the provider's precision capabilities, quality control methods, material expertise, and a strong track record in similar projects. Case studies and customer testimonials are essential to verify their success in meeting strict tolerances.
Q: How do CNC machining processes achieve tight tolerances?
A: They achieve tight tolerances through computer-controlled tool paths, high-precision instruments, and real-time monitoring. Advanced technology and rigorous quality control measures ensure even minute deviations are corrected.
Q: What are some common challenges when machining hard-to-cut materials like titanium?
A: Challenges include tool wear, heat generation, and material work hardening. These are mitigated by advanced cutting tools, optimized feed rates, and proper cooling systems to ensure precise cuts and smooth surfaces.
Q: How does multi-axis machining improve production efficiency?
A: Multi-axis machining reduces the need for multiple setups by allowing simultaneous cutting from different angles, which minimizes repositioning errors and speeds up production cycles while improving accuracy.
Q: Why is automation increasingly important in CNC machining?
A: Automation minimizes human error and maintains consistent machining conditions throughout production. Robotic systems and real-time monitoring adjust cutting parameters automatically, leading to improved accuracy and reduced downtime.
Q: How do advancements in CAD/CAM software influence CNC machining precision?
A: Such software enhances design accuracy by simulating tool paths and identifying potential issues before production begins, ensuring that parts closely match design specifications.
Q: Can CNC machining processes be sustainably optimized?
A: Yes, sustainable practices such as optimized tool paths, energy-efficient machinery, and environmentally friendly cutting fluids reduce waste and energy consumption while maintaining high precision.
Final Thoughts
Precision manufacturing through advanced CNC machining techniques empowers you to produce components with unrivaled accuracy and reliability. By embracing multi-axis, Swiss, and EDM machining—and by carefully selecting materials, optimizing processes, and leveraging automation and software integration—you can achieve exceptional quality while reducing production costs. Evaluate CNC machining services based on their technical expertise, quality controls, and proven case studies to ensure that your parts consistently meet the highest precision standards.
Save Manufacturing Costs With Advanced Techniques
Talk to our experts. Our qualified engineers are always happy to answer your questions.