Table Of Contents:
- How to Choose the Right Metal Cutting Service for Your Project Needs
- What Are Your Project Requirements for Metal Cutting?
- Which Metal Cutting Methods Best Fit Your Project Needs?
- How Do Different Metal Types Impact Your Cutting Service Choice?
- What Key Factors Should You Consider When Choosing a Metal Cutting Service?
- What Are the Design File Requirements for Metal Cutting Services?
- What Finishing Services Complement Metal Cutting Projects?
- How Can You Evaluate Metal Cutting Service Costs and Get Accurate Quotes?
- Where Can You Find Reliable Metal Cutting Services for Your Industry?
- Frequently Asked Questions
- Final Thoughts
How to Choose the Right Metal Cutting Service for Your Project Needs
In any manufacturing or prototyping project, choosing the right metal cutting service is essential to your overall success. You need a service that not only meets technical specifications but also works within your project’s budget and timeline. This article outlines how to evaluate your project requirements and select a metal cutting provider that meets your specific needs. You will learn about various cutting methods, metal properties, and service considerations that affect your final outcome. Whether you need waterjet cutting services, laser cutting, or CNC machining services, understanding these factors will help you achieve precision, efficiency, and a high-quality finish on your parts.
Below, we break down the discussion into key areas: project requirements, cutting method options, metal-specific issues, service factors, design file requirements, finishing services, cost evaluation, and industry-specific applications.
Transitioning now to the detailed explanation of project requirements, let’s delve into the factors that will steer you toward the optimal cutting solution.
What Are Your Project Requirements for Metal Cutting?
Before contacting a metal cutting service, assess your project’s needs. Start by defining the metal type, tolerances, quantities, and budget. Clarify the specific metal you need to cut since different metals, alloys, and composites require various cutting techniques. For instance, titanium alloys may need slower, more precise cutting to prevent heat damage, while aluminum can be processed faster. Your project's precision and tolerance requirements directly affect the choice of method; a rough cut may work for prototypes, but production parts need tight tolerances and a polished finish.
Also, consider the volume of parts required. Large production runs may benefit from high-speed CNC machines or automated laser systems, whereas a small custom project might be better suited for a manual waterjet cutter. Project urgency and budget are key factors as well. Some methods, like plasma cutting, can offer cost savings for bulk jobs but may fall short in precision needed for delicate components, while CNC cutting methods typically provide high accuracy at higher turnaround times and costs.
Finally, account for any additional processing steps such as finishing, bending, or coating. Combined, these factors create a complete picture of your project's needs, guiding you toward the right metal cutting service.
Which Metal Cutting Methods Best Fit Your Project Needs?
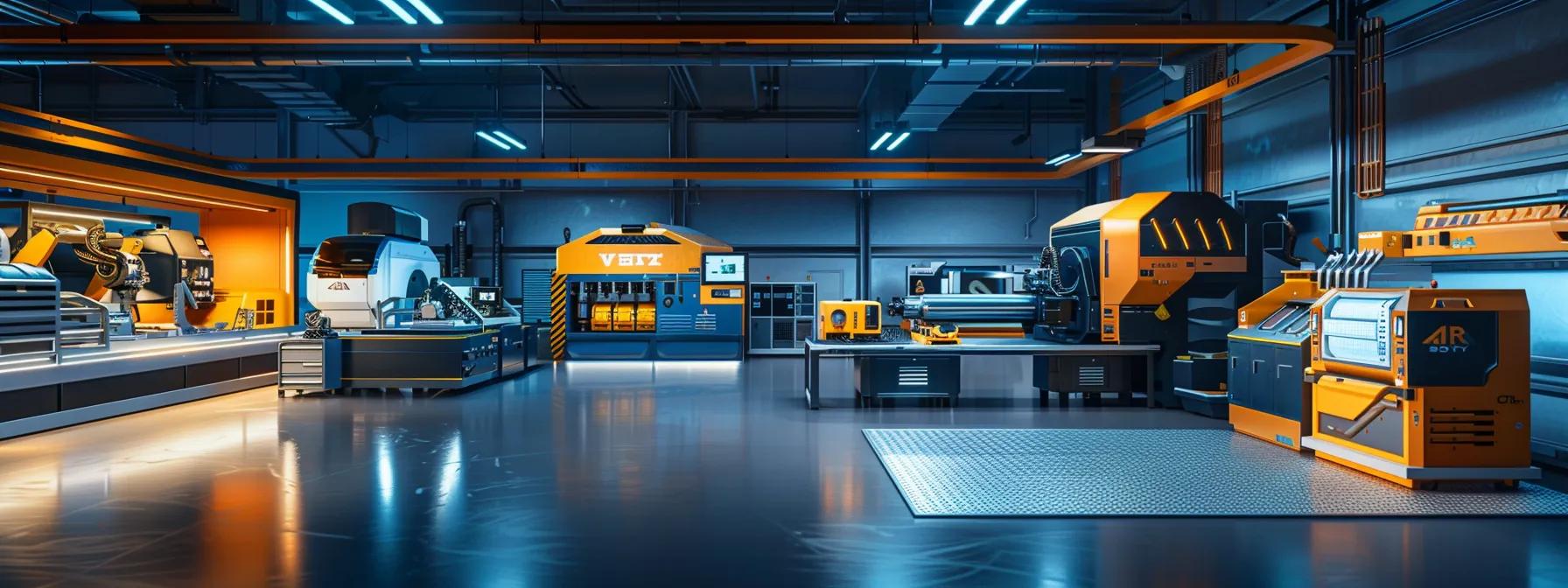
The choice of metal cutting method depends on the metal type and the desired finish quality. Below are details on CNC cutting, laser cutting, waterjet cutting, and plasma cutting, and how each aligns with your project requirements.
What Are the Advantages and Applications of CNC Cutting?
CNC (Computer Numerical Control) cutting offers exceptional accuracy and repeatability through computer-controlled operations. This method is highly effective for intricate designs and precision engineering found in tool steel or titanium alloy prototypes.
Key benefits of CNC cutting include fast production on large runs, consistent part quality, and decreased human error. Tolerances can be as tight as ±0.01 mm, making this ideal for aerospace or automotive parts. In addition, CNC services adapt to materials like steel, aluminum, copper, and more without compromising quality. Some providers even offer secondary processes like deburring or automated finishing to ensure the part is production-ready. These attributes make CNC cutting a top option when precision metal cutting and repeatability are crucial.
How Does Laser Cutting Work and When Is It Ideal?
Laser cutting uses a high-power laser beam that melts, burns, or vaporizes metal along a pre-programmed path. It is ideal when high precision and smooth finishes are required. Laser cutting produces clean edges with minimal kerf width and excels at intricate designs, making it popular in medical device manufacturing and decorative metal fabrication.
Although heat accumulation can sometimes cause slight deformations, advanced cooling techniques and controlled beam parameters ensure most projects achieve high quality finishes. Laser cutting is versatile enough for steel, aluminum, and certain stainless steels. Fast turnaround times and cost-effectiveness when precision is paramount make it attractive for prototyping and small-scale production.
What Makes Waterjet Cutting Versatile for Different Materials?
Waterjet cutting uses a high-pressure stream of water mixed with abrasive particles to slice through metals without generating significant heat. This method is exceptionally versatile, cutting virtually any metal without affecting its integrity.
A major advantage is minimal thermal distortion, which is especially important for sensitive materials like certain tool steels or plastics. Waterjet cutting adapts to thick metal plates as well as delicate materials, preserving the intrinsic properties of the metal. In addition, these systems are known for their environmental benefits, generating less waste and using recyclable water and abrasives. For projects requiring intricate shapes with a clean finish, waterjet cutting is an excellent option.
When Is Plasma Cutting the Most Cost-Effective Option?
Plasma cutting directs a high-velocity jet of ionized gas through conductive metals, slicing them quickly and efficiently. It is typically the most cost-effective option for thicker metals or large-scale rough cutting. Known for rapid speeds and lower operational costs, plasma cutting is ideal when precision is secondary.
This method suits large sheets of metal or support structures where a slightly rough edge is acceptable. While not as smooth as laser or CNC cuts, plasma cutting excels in applications such as automotive or shipbuilding, particularly when used with post-processing to smooth edges. It delivers a balance of cost and performance in high-volume settings.
How Do Different Metal Types Impact Your Cutting Service Choice?
Each metal or alloy has unique properties that dictate the best cutting approach. Evaluating these properties is critical as they influence the choice of method, tools, and process parameters.
What Are the Key Properties of Steel for Metal Cutting?
Steel is prevalent in manufacturing due to its high tensile strength, durability, and versatility. When cutting steel, consider properties such as hardness, thickness, and composition. Typically, steel requires high precision and robust tool systems, often favoring CNC or waterjet cutting for complex geometries. For example, carbon steel is widely used in automotive and construction due to its strength, while stainless steel finds use in corrosion-resistant applications. Factors like abrasion resistance, thermal conductivity, and ductility affect cutting speeds and tool selection. A clear understanding of steel’s properties helps ensure minimal waste and high cutting efficiency.
How Does Aluminum Affect Cutting Method Selection?
Aluminum is favored in aerospace, automotive, and electronics manufacturing due to its lightweight and high thermal conductivity. Its softness and low melting point allow faster cutting methods, such as laser cutting and CNC machining, which deliver high precision without significant thermal damage. However, aluminum’s reflective surface may require power adjustments during laser cutting to avoid warping. Alternatively, waterjet cutting is ideal since it avoids heat distortion altogether. Manufacturers often use specialized CNC programs for intricate aluminum parts, thus ensuring effective processing and high precision.
What Should You Know About Stainless Steel Cutting?
Stainless steel, known for corrosion resistance and durability, presents challenges due to its high hardness and low thermal conductivity. It typically requires robust cutting techniques to maintain edge quality and precision. Laser and waterjet cutting are preferred for stainless steel; both work efficiently without compromising the material’s properties. Managing cutting speed, kerf width, and potential post-cut heat treatment is essential when working with high chromium content that provides stainless steel its corrosion resistance. Clear communication of specifications ensures optimal cutting parameters.
How Are Copper and Brass Best Cut for Your Project?
Copper and brass are prized for their conductivity and aesthetic appeal but require careful cutting to avoid deformation and oxidation. Laser cutting is effective for brass because of high precision, while waterjet cutting is ideal for copper since it minimizes heat buildup that might alter color or performance. Maintaining surface finish and dimensional accuracy is vital, especially for decorative or electrical components. The right cooling techniques and precise equipment settings are critical to preserving the quality of copper and brass parts.
What Key Factors Should You Consider When Choosing a Metal Cutting Service?
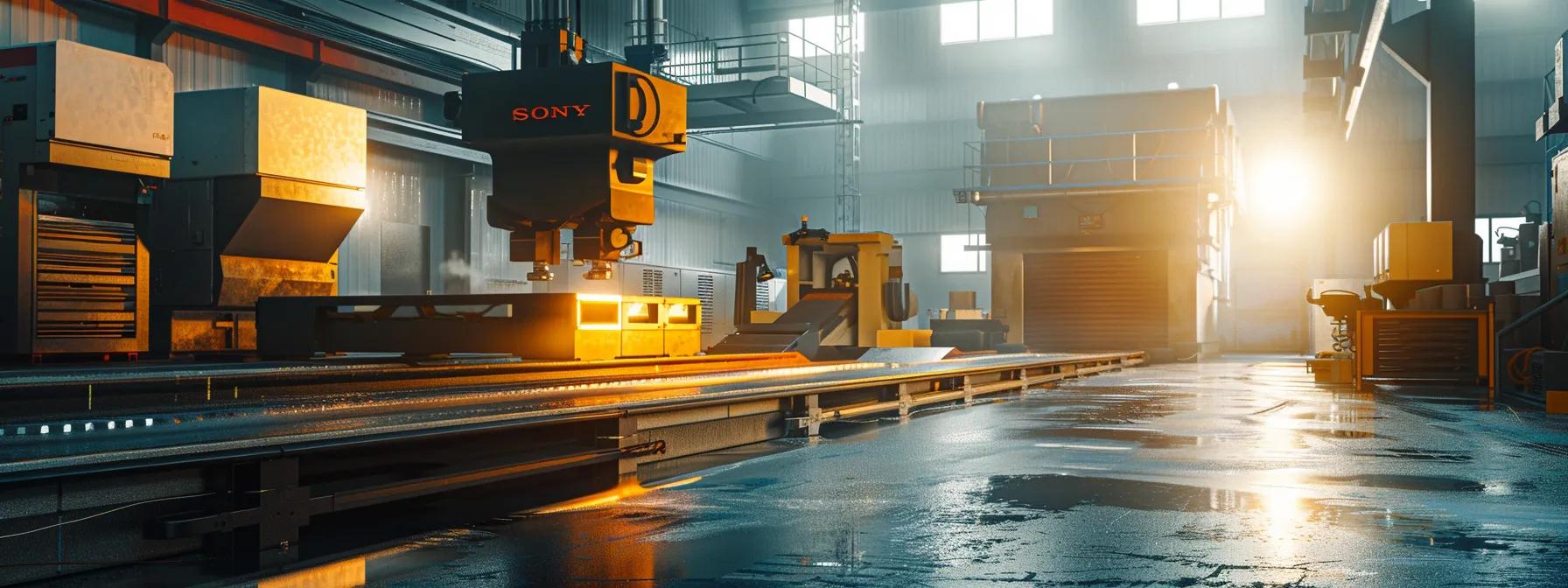
Do you need help to find best metal cutting services?
Talk to our experts. Our qualified engineers are always happy to answer your questions.
Selecting a metal cutting service involves more than technical specifications. Key factors include the provider’s experience, cutting capabilities, quality control, turnaround time, pricing, and customer service. These elements together determine the reliability and suitability of a service provider.
Why Is Experience and Expertise Critical in Metal Cutting?
Experience and expertise are crucial since seasoned providers better handle complex projects and ensure consistent quality. Skilled service providers understand the nuances of different metal types and cutting methods, such as switching between CNC, waterjet, or laser cutting. Their expertise helps reduce errors, minimize wastage, and improve turnaround times. Providers with modern machinery and industry-tested processes offer innovative solutions that protect intellectual property and maintain precise production standards.
How Do Cutting Capabilities and Material Availability Affect Your Choice?
A provider’s cutting capabilities—the range of techniques and equipment they offer—are important for handling various metal types and complexities. Comprehensive services that include CNC, waterjet, laser, and plasma cutting ensure a suitable method is available for any project. In addition, having immediate access to different metal grades through efficient material management can reduce lead times and production delays, and support additional finishing processes.
What Role Does Quality Control Play in Service Selection?
Quality control is fundamental for ensuring that each part meets required specifications and industry standards. This involves precise measurements, systematic testing, and adherence to certifications such as ISO 13485 for medical devices. Providers with stringent quality control use calibrated tools and automated inspections to reduce defects and prevent costly rework, ensuring reliable and consistent production.
How Important Are Turnaround Time and Pricing?
Turnaround time and pricing directly affect your project schedule and overall cost. A balance between cost and speed is essential; faster turnarounds may come at a premium, while lower prices might result in longer lead times or reduced quality. It is important to compare quotes and understand what each provider includes in their pricing model, whether it’s material costs, labor, setup fees, or post-cut finishing. Transparent pricing and reliable turnaround times are key to staying on schedule without sacrificing quality.
Why Should Customer Service Influence Your Decision?
Excellent customer service enhances technical expertise by offering dedicated support throughout the project. Prompt communication, clear responses to design file queries, regular updates, and efficient handling of unforeseen issues ensure that your project is closely monitored. Providers that excel in customer service are proactive in discussing changes and improvements, which can prevent costly revisions and help keep your project on track.
What Are the Design File Requirements for Metal Cutting Services?
Submitting precise and compatible design files is essential for successful metal cutting. These files act as blueprints, ensuring each cut is executed accurately.
Which File Formats Are Accepted for Metal Cutting Projects?
Common file formats for metal cutting services include DXF, DWG, IGES, and STEP. These industry-standard formats carry the detailed geometric information needed for CNC, laser, and waterjet cutting. Always verify with your provider which file types they support to ensure smooth processing and minimal conversion errors.
What Design Considerations Ensure Accurate Cutting?
Accurate metal cutting requires design standards, tolerances, and clear annotations. Designers should specify exact dimensions, hole placements, and edge finishes in files drawn to scale. It is important to include detailed tolerances and account for kerf—the material removed by the cutting process. Advanced CAD software can simulate cuts to adjust dimensions accordingly. Clear, organized files help prevent mistakes and reduce processing time, ultimately saving costs.
What Finishing Services Complement Metal Cutting Projects?
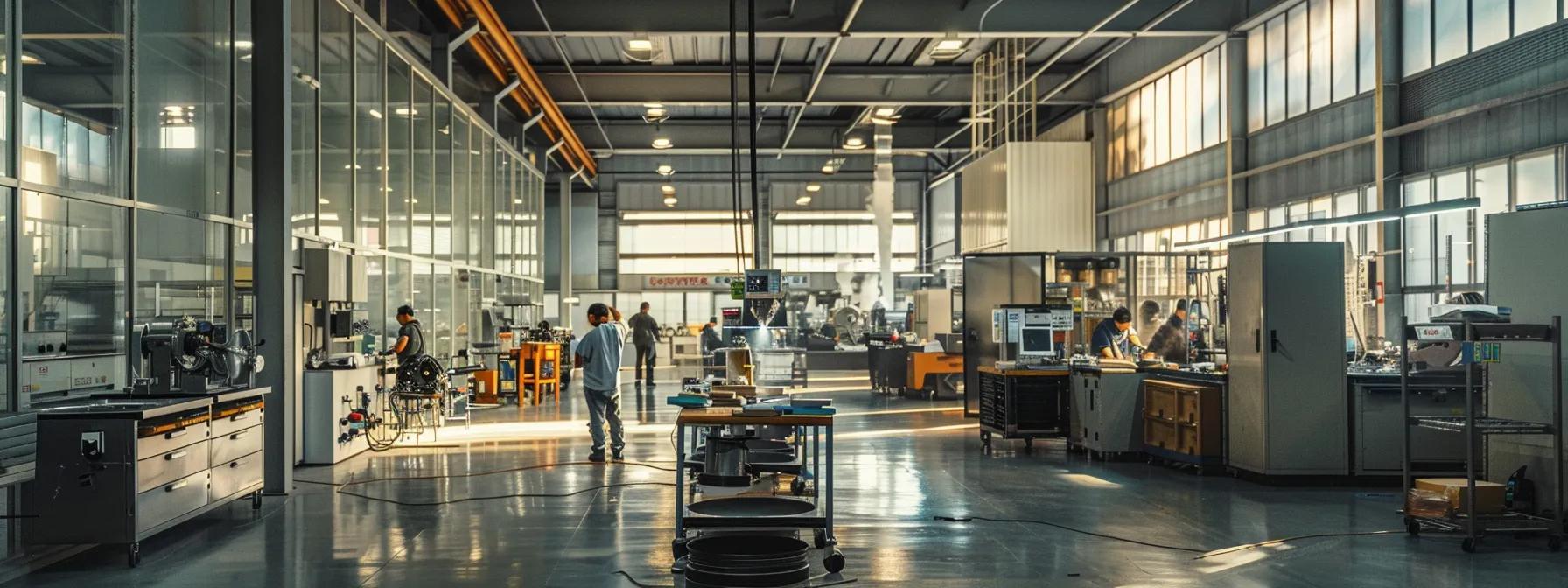
After cutting, finishing processes enhance the usability and appearance of metal parts. Finishing services add value, improve durability, and protect against environmental stress.
How Do Painting, Powder Coating, and Plating Enhance Metal Parts?
Processes such as painting, powder coating, and plating improve durability by applying a protective layer against corrosion, abrasion, and chemical exposure. Painting offers a wide range of colors and finishing options, while powder coating delivers a robust and even finish resistant to scratches. Plating, including gold or chrome, enhances conductivity, reduces friction, and creates a high-gloss appearance. Integrating finishing services with metal cutting helps streamline production and meet industry-standard quality.
How Can You Evaluate Metal Cutting Service Costs and Get Accurate Quotes?
Evaluating costs involves understanding the factors that influence pricing so you can budget effectively and secure competitive quotes. A transparent cost evaluation approach is essential for preventing overruns and ensuring value for money.
ALSO READ: Understanding Pricing in Precision Metal Parts Manufacturing Services
What Factors Influence Metal Cutting Pricing?
Key pricing factors include material type, thickness, design complexity, volume of cuts, and post-processing requirements. For instance, cutting a thick stainless steel plate with intricate details will cost more than a simple aluminum sheet. The choice of cutting method also matters; a laser cut may charge per machine minute, while waterjet pricing could be based on material area. Additional considerations include labor, machine setup, and waste management.
How Can You Use Cost Guides or Calculators for Budgeting?
Many providers offer online tools that allow you to input project specifics—such as material type, thickness, geometry, and volume—to generate an approximate quote. These calculators help improve budgeting accuracy and allow you to compare different providers on a level playing field. Discussing preliminary estimates with the provider can also lead to customized solutions and potential cost savings.
Below is an example table summarizing key factors influencing metal cutting pricing:
Factor | Attribute | Impact on Cost | Example |
---|
Material Type | Steel, Aluminum, etc. | Varies by hardness and quality | High-grade stainless steel costs more |
Thickness | Measured in mm/inches | Thicker materials require more time | 10 mm steel vs. 2 mm aluminum |
Design Complexity | Geometrics and tolerances | More complexity increases machine time | Intricate patterns increase cost |
Cutting Method | CNC, Laser, Waterjet, Plasma | Influences speed and precision | Laser cutting is more precise |
Volume/Quantity | Number of parts | Bulk orders may lower unit cost | High volume reduces per-part cost |
Post-Processing | Finishing treatments | Additional surface processes add cost | Powder coating, painting |
This table helps you understand what drives your budget and where cost optimizations might be possible while maintaining quality.
Do you need help to calculate custom metal cutting cost?
Talk to our experts. Our qualified engineers are always happy to answer your questions.
Where Can You Find Reliable Metal Cutting Services for Your Industry?
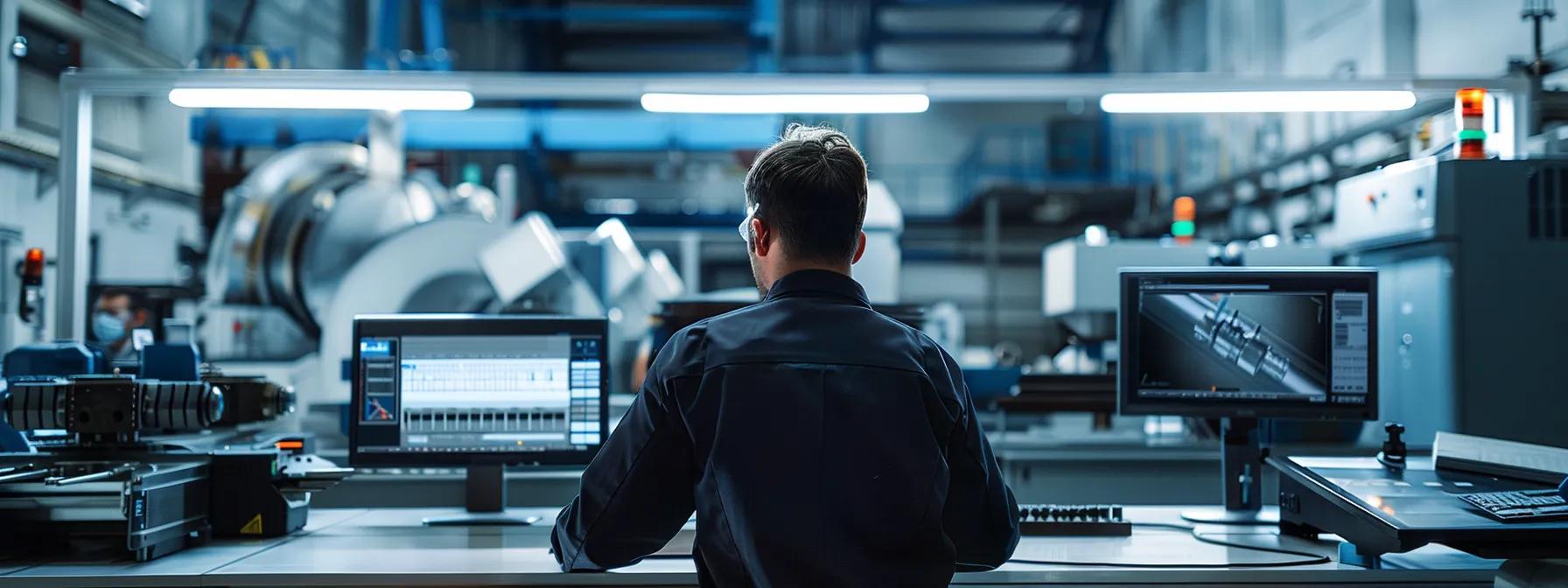
Selecting a metal cutting service requires understanding your industry’s specific requirements. Whether your project is in aerospace, automotive, construction, or manufacturing, each sector has unique demands that must be met.
How Does Metal Cutting Differ for Aerospace Applications?
In aerospace, precision and material integrity are paramount. Components must adhere to strict tolerances, stringent quality control, and rigorous testing. Providers serving aerospace typically use advanced CNC, laser, and waterjet cutting to produce defect-free parts. Specialized finishing processes, such as high-grade anodizing or protective coatings, are also common. Certifications like AS9100 and ISO 9001 help ensure that every cut meets the necessary standards for flight.
What Are the Metal Cutting Requirements in Automotive Projects?
Automotive manufacturing often demands high-volume production with tight tolerances and consistent repeatability. CNC and plasma cutting are widely used for components such as body panels and engine parts. In the automotive sector, parts usually require finishing treatments like painting or plating to improve durability and performance. Fast turnaround times and cost-effective pricing are critical in managing both prototyping and mass production.
How Is Metal Cutting Applied in Construction and Manufacturing?
In construction and general manufacturing, metal cutting services are used to produce frames, supports, and custom components. These sectors require a blend of speed, versatility, and cost efficiency. Plasma and waterjet cutting are popular for processing thick materials and large formats, while CNC or laser cutting offers the precision needed for delicate assemblies. Strong quality control and reliable delivery times are essential for ensuring that parts fit together correctly in final assemblies.
Below is a table comparing key service provider attributes by industry:
Industry | Required Precision | Common Cutting Methods | Quality Certifications | Average Turnaround Time |
---|
Aerospace | High (±0.01 mm) | CNC, Laser, Waterjet | AS9100, ISO 9001 | 2-3 weeks for prototypes |
Automotive | Moderate to High | CNC, Plasma, Laser | IATF 16949 | 1-2 weeks for production runs |
Construction | Moderate | Plasma, Waterjet | ISO 3834 | 2-4 weeks depending on size |
Manufacturing | Variable | CNC, Laser, Waterjet | ISO 9001, Industry Standards | 1-3 weeks typically |
This table provides insight into how different industries influence the choice of metal cutting service, helping you match your project requirements with the right expertise.
Final Thoughts
In conclusion, selecting the right metal cutting service requires careful evaluation of your project requirements, metal properties, and available cutting methods. Consider technical aspects such as precision, tolerance, and metal type, along with operational factors like turnaround time, cost, and customer service. By understanding the nuances of CNC, laser, waterjet, and plasma cutting and matching these methods with your material needs, you can achieve high-quality results that meet your project’s demands. A well-informed decision based on detailed requirements and reliable service providers is key to a successful outcome.
Frequently Asked Questions
All The Above Discussions Are Answered At A Glance
Q: How do I determine which metal cutting method is best for my project?
A: Evaluate your project’s material type, tolerance, and finish requirements. For high precision and intricate designs, consider CNC or laser cutting; for materials prone to heat damage, waterjet cutting is ideal. Assess production volume and turnaround time, and provide detailed design files to ensure the correct method is chosen.
Q: What file formats are most commonly accepted by metal cutting services?
A: Most services accept DXF, DWG, IGES, or STEP formats, which contain all necessary dimensional and geometric information. Always verify with your provider to ensure file compatibility.
Q: How important is quality control in the metal cutting process?
A: Quality control is crucial to ensure parts meet precise specifications. Automated inspections and calibrated measurement tools help maintain consistency and reduce errors, leading to better reliability and fewer costly flaws.
Q: Can I get an accurate cost estimate for metal cutting services online?
A: Yes. Many providers offer online cost calculators where you enter project details—such as material type, thickness, design complexity, and volume—to generate an approximate quote. This helps with budgeting and comparison.
Q: How does the choice of metal affect the cutting method?
A: Metal properties like hardness, thermal conductivity, and thickness influence the best cutting method. Aluminum’s softness and high thermal conductivity, for example, make it ideal for laser and CNC cutting, while thicker or heat-sensitive materials might be better suited for waterjet or plasma cutting.
Q: What turnaround time should I expect for a standard metal cutting project?
A: Turnaround time depends on design complexity, material type, and volume. Prototypes may take one to three weeks, while larger production runs could require more time. Discuss deadlines with your provider to ensure they meet your schedule.
Q: Do finishing services like painting or plating add significant cost to metal cutting projects?
A: While they do add to the overall cost, finishing services enhance durability and aesthetics. Processes such as powder coating, painting, and plating protect metal parts and can reduce long-term maintenance expenses, balancing functionality with visual appeal.