Table Of Contents:
- Precision Machining Services for Superior Metal Parts
- What Are Precision Machining Services and How Do They Enhance Metal Part Quality?
- Which Materials Are Best Suited for Precision Machining of Metal Parts?
- How Are Precision Machining Tolerances Defined and Achieved?
- Which Industries Benefit Most From Precision Machining Services?
- What Factors Influence the Cost of Precision Machining Services for Metal Parts?
- Why Choose HLH Sheet Metal for Your Precision Machining Needs?
- How Can You Get Started With Precision Machining Services for Your Metal Parts?
- Detailed Comparison Table: Material Properties, Machining Tolerances, and Cost Impact
- Frequently Asked Questions
- Final Thoughts
Precision Machining Services for Superior Metal Parts
Precision machining services represent specialized manufacturing processes that produce metal parts with extremely high accuracy and surface finish. In custom parts production, every micron matters, and these services ensure each component meets strict tolerance and quality standards. Techniques such as CNC milling, turning, drilling, and multi-axis machining rely on computer numerical control systems for reproducibility. Whether developing components for aerospace, automotive, or medical devices, precision machining guarantees consistency, minimal waste, and rapid turnaround. This article outlines key machining processes, material selection importance, the technology behind tight tolerances, and why industries rely on precision machining for superior metal parts. By the end, you will understand the benefits of engaging a specialized partner like HLH Sheet Metal for your machining needs.
What Are Precision Machining Services and How Do They Enhance Metal Part Quality?
Precision machining services use computer-controlled equipment to produce metal parts with enhanced quality, repeatability, and dimensional accuracy. Designed to cut, shape, and finish materials to meet specialized engineering requirements, these services achieve tolerances as tight as ±0.001 inches. This precision is critical for components that must fit together seamlessly, where even minor deviations can compromise performance or safety. By controlling the machining environment with stable fixtures, precise tools, and advanced sensors, these services eliminate inconsistencies typical of manual methods, ensuring every part meets or exceeds quality assurance and functionality expectations.
What Is Precision Machining and Its Key Processes?
Precision machining is the high-accuracy, computer-controlled process of manufacturing metal parts with exact tolerances. Key processes include CNC milling, turning, drilling, and finishing. In CNC milling, rotating cutters remove material from a stationary workpiece; in CNC turning, the workpiece rotates against fixed cutting tools to create symmetrical shapes. Processes such as electrical discharge machining (EDM) and grinding further refine surface finish and dimensions. Precise programming and automated control enable large-volume production to match the quality of one-off prototypes. Specialized tooling and fixtures reduce variation and ensure products meet demanding specifications in industries sensitive to fatigue, stress, and performance.
How Do CNC Milling and CNC Turning Improve Metal Part Accuracy?
CNC milling and turning form the core of precision machining by using automated, computer-controlled actions to shape parts. CNC milling employs multi-axis cutting where tools remove material uniformly from various directions, whereas CNC turning rotates the workpiece while fixed tools cut along its diameter. Automation minimizes human error and delivers intricate geometries with tolerances often within microns. High-quality cutting tools and coolant systems maintain optimal heat control and reduce vibration, ensuring parts meet dimensional requirements and possess excellent surface finishes. This level of precision is essential to prevent misalignment or failure in assemblies.
What Are the Benefits of Precision Machining for Custom Metal Parts?
Precision machining offers numerous advantages. It delivers outstanding accuracy and repeatability, ensuring every part is nearly identical—essential for small-batch production or prototypes. Using advanced techniques reduces material wastage and allows for innovative, complex geometries that enhance performance without compromising design. Additionally, precision machining improves finished product efficiency by reducing friction, ensuring secure fittings, and enhancing surface integrity. As industries demand increasingly sophisticated products, these services contribute to greater reliability, higher safety standards, and longer product lifespans.
Which Materials Are Best Suited for Precision Machining of Metal Parts?
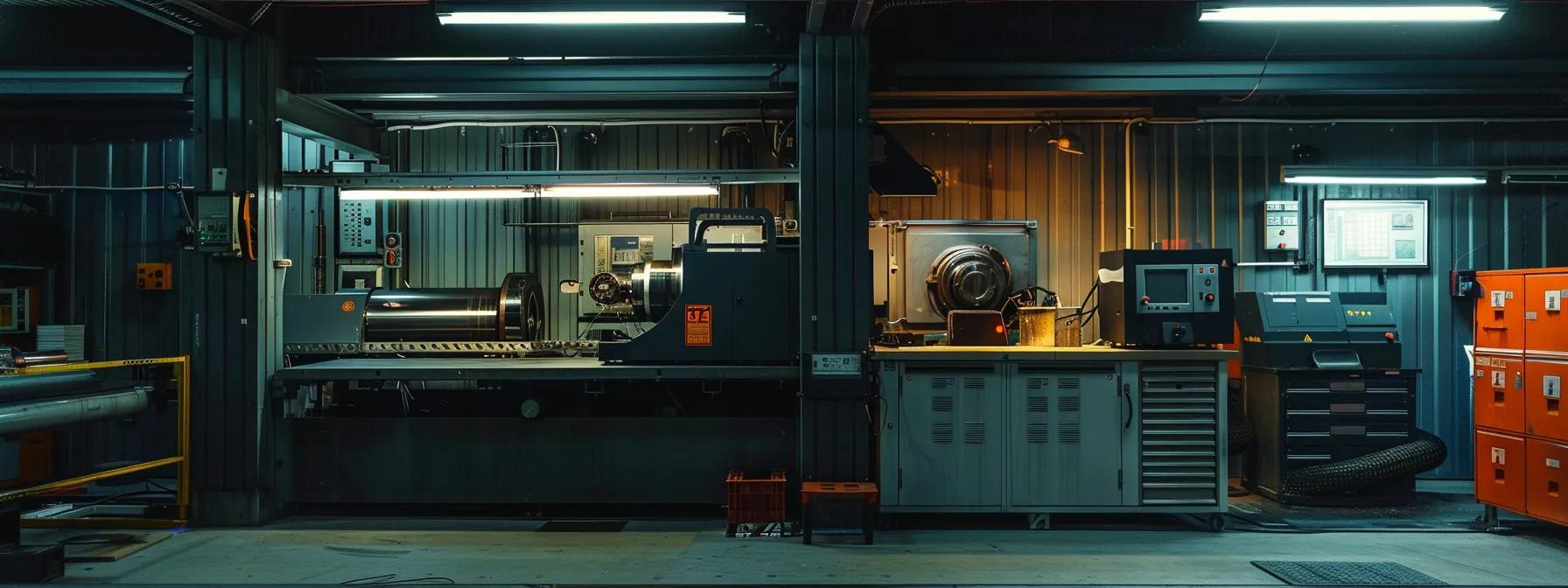
Choosing the right material is as crucial as precise machining methods since metals respond differently to cutting, heat, and stress. Commonly used materials include aluminum, steel, and titanium, each with unique properties affecting machining performance and durability. Selecting the appropriate raw material provides optimal functionality and efficient processing. Manufacturers also use exotic alloys for applications requiring extraordinary wear, thermal stress, or corrosion resistance.
What Are the Properties of Aluminum, Steel, and Titanium in Machining?
Aluminum is lightweight, highly machinable, and offers an excellent strength-to-weight ratio, making it ideal for aerospace and automotive applications. Its softness enables faster machining, though additional coatings might be needed for durability. Steel—especially stainless or alloy types—provides robust strength, wear resistance, and high-temperature tolerance but requires careful tool selection and speed control to manage heat buildup. Titanium, with its superior strength, corrosion resistance, and biocompatibility, is indispensable in aerospace and medical devices. However, its toughness and low thermal conductivity demand specialized tools and machining parameters to prevent wear and maintain precision.
How Does Material Selection Impact Machining Precision and Durability?
Material characteristics such as hardness, thermal expansion, and alloy composition directly influence machining parameters like cutting speed, feed rate, and coolant application. Softer metals like aluminum need different tooling compared to materials like titanium or hardened steels. These intrinsic properties affect chip formation and cutting forces, making the correct material choice essential for meeting tolerances and ensuring long-term durability, particularly in industries where component failure can cause significant operational downtime or safety hazards.
What Exotic Alloys Are Used in Advanced Precision Machining?
Beyond aluminum, steel, and titanium, advanced precision machining often involves exotic alloys like Inconel, Hastelloy, and other superalloys. Inconel, a nickel-chromium alloy, is very strong and oxidation-resistant, making it ideal for aerospace engine parts despite being challenging to machine. Hastelloy offers exceptional corrosion resistance for chemical processing applications. These materials may require specialized tools and machining parameters, underlining the sophistication and expertise needed to work with such exotic alloys.
ALSO READ: Advanced Materials in Sheet Metal Fabrication Pushing the Boundaries
How Are Precision Machining Tolerances Defined and Achieved?
Precision machining tolerances are the allowable deviations from specified dimensions that ensure parts fit together properly. These tolerances are defined by engineering drawings and international standards, ranging from a few microns to several thousandths of an inch based on the part’s function and industry requirements. Achieving such precision requires advanced CNC technology, rigorous planning, and continuous monitoring. Feedback systems and in-process measurement tools help ensure each component meets its strict specifications.
What Are Typical Tolerance Ranges in Precision Machining?
Tolerance ranges in precision machining vary with part complexity and material. For high-end aerospace or medical components, tolerances are typically between ±0.001 and ±0.005 inches. In less critical applications, they may be looser—around ±0.01 inches. These ranges depend on the intended function of the part, assembly needs, and environmental factors like temperature and load. Establishing tolerance ranges early in the design phase allows manufacturers to calibrate equipment and select appropriate cutting parameters.
How Do CNC Technologies Ensure Consistent Dimensional Accuracy?
Modern CNC machines use pre-programmed software, precise motion control, and sensors to maintain consistent dimensional accuracy. They continuously monitor the cutting process and adjust feed rates and tool positions in real time to correct any deviations. Techniques like tool path optimization and adaptive control, combined with laser measurement and touch probe systems, allow for immediate verification of dimensions and rapid corrections, ensuring ongoing quality and precision.
Why Are Tight Tolerances Essential for Superior Metal Parts?
Tight tolerances ensure that components fit seamlessly without additional adjustments. In high-performance systems such as aerospace engines, automotive transmissions, and medical devices, even minor deviations can lead to misalignment, energy loss, or failure. Consistent dimensions improve overall product performance, safety, and longevity, while reducing maintenance and error rates in assembly lines.
Which Industries Benefit Most From Precision Machining Services?
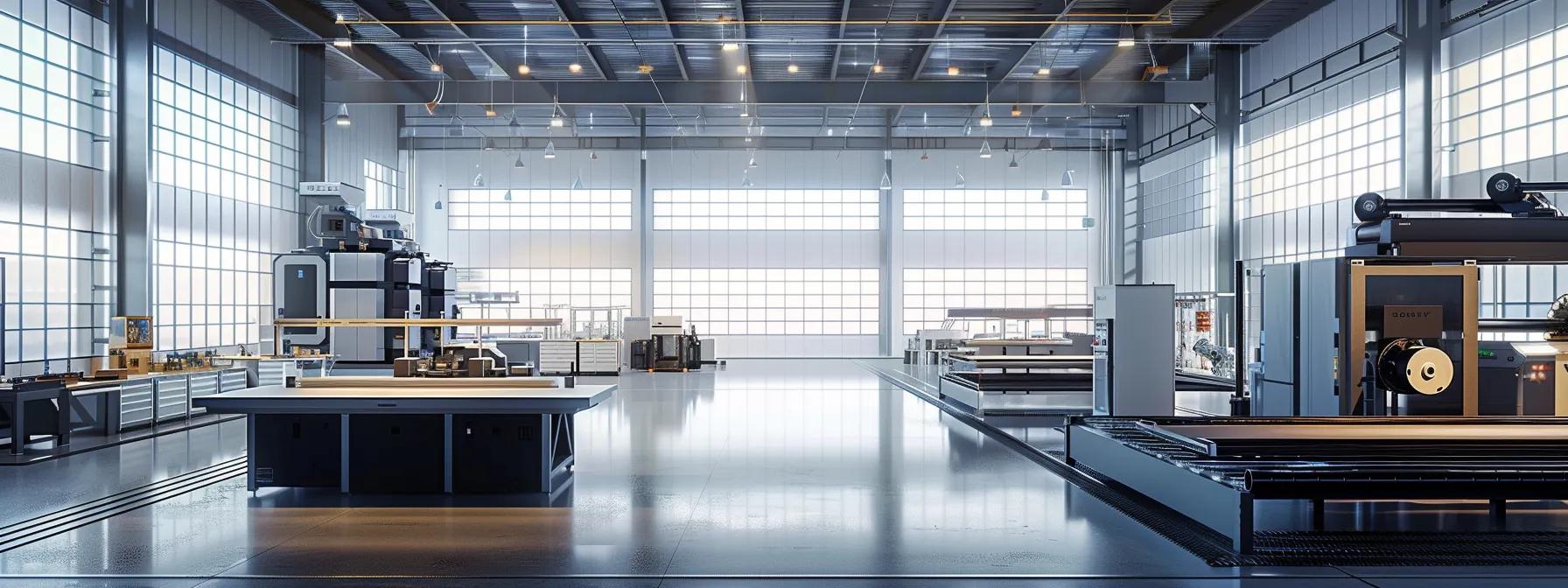
Precision machining is vital across industries that require high-quality, custom metal parts. Aerospace, automotive, and medical device manufacturing are among the foremost sectors that depend on precision machining for performance and safety. These industries benefit from parts that meet stringent dimensional and surface finish requirements, ultimately enhancing system reliability, durability, and overall safety. Advanced CNC technologies and specialized cutting techniques make it possible to address industry-specific challenges efficiently.
How Does Precision Machining Serve the Aerospace Industry?
In aerospace, precision machining is crucial for manufacturing components that operate under extreme conditions. Aircraft engines, airframes, and control systems require parts with exceptionally high tolerances and durability. Machining exotic alloys like Inconel and titanium, which can withstand high temperatures and pressures, is common. Continuous monitoring and strict quality control ensure parts meet performance and weight specifications, contributing to enhanced safety and efficiency in aerospace systems.
What Are the Precision Machining Needs in Automotive Manufacturing?
The automotive industry benefits from precision machining by receiving high-quality parts that enhance engine performance, fuel efficiency, and safety. Components such as transmission gears, engine blocks, and suspension parts require high dimensional accuracy for smooth operation. Precision machining supports rapid prototyping and low-volume production for new technologies like electric drivetrains and autonomous systems, while also addressing the industry’s focus on lightweight designs through materials like aluminum and high-strength steel.
Why Is Precision Machining Critical for Medical Device Production?
For medical devices, precision machining is essential to produce components that meet strict regulatory standards and ensure patient safety. Implants, surgical instruments, and diagnostic equipment require precise, complex geometries and smooth surface finishes for biocompatibility. Enhanced machining capabilities support innovation in minimally invasive devices and diagnostic tools, ultimately leading to improved patient outcomes and safer, more reliable medical devices.
What Factors Influence the Cost of Precision Machining Services for Metal Parts?
The cost of precision machining depends on factors such as material selection, part complexity, production volume, and the technological capabilities of the service provider. The need for high precision drives costs related to complex machining processes, time-intensive programming, specialized tooling, and high-resolution measurement systems. Rapid prototyping and low-volume production often have different pricing structures compared to full-scale manufacturing. Clients must balance these factors with quality and lead time objectives to understand overall costs.
How Do Material Types Affect Machining Costs?
Material choice significantly impacts machining costs. Softer metals like aluminum result in lower tool wear and faster cutting speeds, reducing cost. In contrast, high-strength metals like titanium or hardened steel require slower speeds, enhanced cooling systems, and specialized tools, thereby increasing costs. Exotic alloys may add extra processing steps and handling, further pushing up expenses. Understanding these differences helps balance performance needs with budget constraints.
What Role Do Complexity and Volume Play in Pricing?
Complex part geometries that involve intricate features require extensive programming, custom tooling, and longer machine time, thus increasing costs. Conversely, high production volumes can result in economies of scale through streamlined processes and improved efficiency, lowering the per-unit cost. However, low-volume or prototype runs often incur higher setup costs and longer lead times, leading to greater expense per part.
How Does Advanced Technology Affect Service Pricing?
Advanced CNC machinery and automated measurement systems improve accuracy and production speed but come with higher capital and maintenance costs. These premium technologies enable tighter tolerances and better surface finishes, reflecting in the overall cost of machining services. Additionally, digital systems for project tracking, quality control, and rapid prototyping boost productivity—factors that collectively influence pricing.
ALSO READ: What Strategies Help Manage Costs in Precision Metal Fabrication?
Why Choose HLH Sheet Metal for Your Precision Machining Needs?
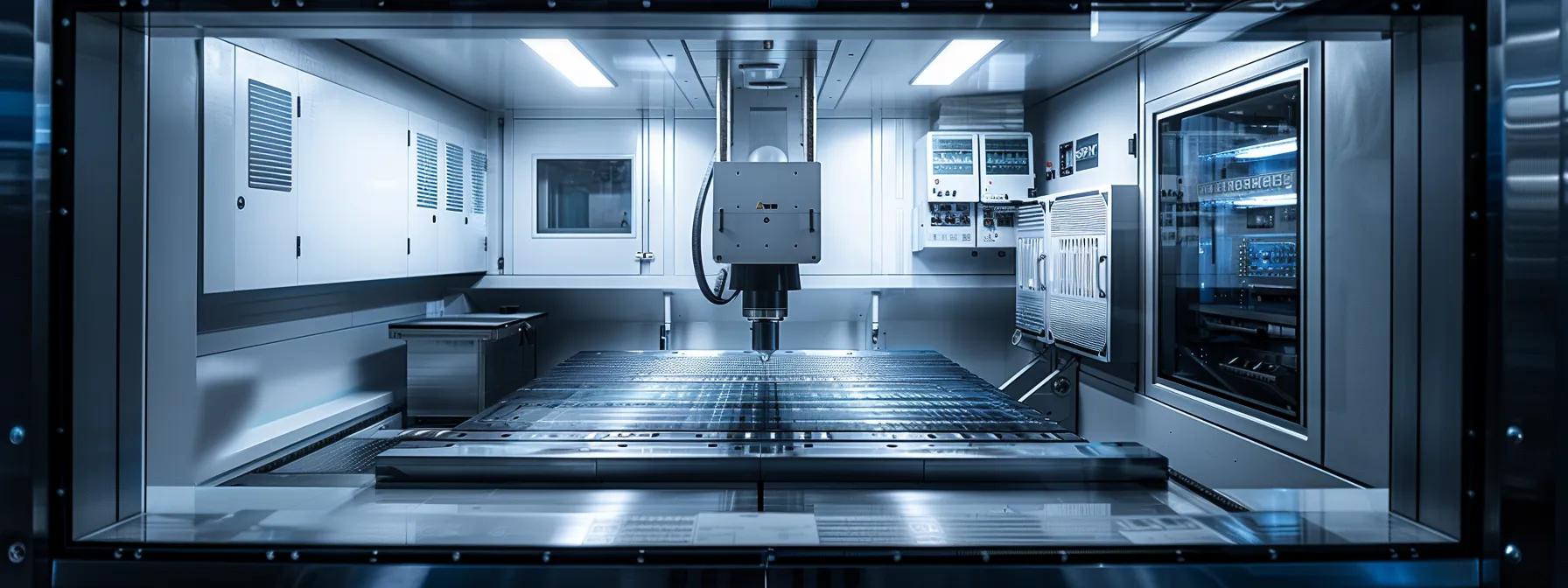
HLH Sheet Metal is a technology-driven partner committed to delivering outstanding accuracy and quality across industries. By leveraging state-of-the-art CNC technology, skilled machinists, and rigorous quality control, we ensure every custom metal part meets stringent specifications. Their focus on innovation and customer satisfaction positions them as a leader in the precision machining market for projects ranging from low-volume prototypes to high-volume production runs.
How Does HLH Sheet Metal Ensure Exceptional Accuracy and Quality?
HLH Sheet Metal combines advanced CNC machines with rigorous process controls and real-time measurement systems. Our quality assurance includes multiple checkpoints during production, using laser measurement and digital calipers for final verification. High-grade tooling and optimized cutting parameters tailored to materials such as tool steel, titanium, and exotic alloys minimize deviations, guaranteeing parts meet the tight tolerances demanded by aerospace and medical sectors.
What Customization Options Are Available for Metal Parts?
At HLH Sheet Metal, customization is central. Options span multiple machining processes, surface finishes, and material treatments to tailor parts to exact specifications. Services include CNC milling, turning, EDM, grinding, and specialized coating such as anodizing and chromate conversion coating. Customers can also request design modifications to enhance part integration in complex assemblies, supporting both rapid prototyping and large-scale production.
Which Advanced Technologies Does HLH Sheet Metal Use?
HLH Sheet Metal employs a suite of advanced technologies, including multi-axis CNC machines and modern CAD/CAM software for precise programming and simulation. Real-time process monitoring, automated tool change systems, and advanced cooling technologies further boost accuracy and reduce cycle times. These innovations ensure every custom metal part meets the highest industry standards.
How Can You Get Started With Precision Machining Services for Your Metal Parts?
Starting with precision machining services is straightforward. Engineers, product designers, and procurement managers can easily request a quote through our online portal or by phone. Discussing project requirements leads to a comprehensive proposal that details materials, production volume, lead times, and costs. This customer-focused process ensures a balance between performance, precision, and cost efficiency.
What Is the Process for Requesting a Quote or Consultation?
To begin your project, contact us via our online portal or phone. Provide technical specifications, preferred materials, and design drawings. The team reviews the details, identifies the optimal machining process, and discusses any necessary customization. A detailed quote then outlines all costs—including setup, machine time, finishing, and quality assurance—ensuring transparency and timely project completion within budget.
What Information Should You Provide for Accurate Project Estimates?
Accurate project estimates require detailed design documents, including CAD files and technical drawings. Provide information on tolerances, surface finish specifications, material type, desired quantities, and any special finishing processes. Clear communication regarding deadlines and budget constraints helps tailor the proposal to your specific needs, leading to more precise cost predictions and smoother production.
How Does HLH Sheet Metal Support Project Management and Delivery?
We supports project management with integrated digital tracking systems and regular client communications. From project initiation to delivery, you receive progress reports and updates. Advanced scheduling aligns production with deadlines, and quality control teams perform in-line and final inspections to verify each part. Collaborative platforms allow for review of interim results and prompt feedback, ensuring timely, reliable delivery.
Detailed Comparison Table: Material Properties, Machining Tolerances, and Cost Impact
Before the conclusion, the table below summarizes how different factors influence precision machining outcomes.
Below is a table comparing common materials and factors:
Material | Typical Tolerance Range | Machining Properties | Cost Impact | Preferred Application |
---|
Aluminum | ±0.005 inches or better | High machinability, fast cutting speeds | Lower cost due to ease | Aerospace components, automotive |
Steel | ±0.001-0.005 inches | High strength, requires slow speeds | Moderate cost | Engine parts, transmission gears |
Titanium | ±0.002-0.005 inches | Low thermal conductivity, tough | Higher cost | Medical devices, high-performance |
Inconel (Exotic) | ±0.001-0.003 inches | Extremely tough, requires specialized tools | Premium pricing | Aerospace engine components |
Hastelloy (Exotic) | ±0.001-0.004 inches | Excellent corrosion resistance | Premium pricing | Chemical processing equipment |
The table highlights critical differences in material properties, tolerance ranges, cost impacts, and applications. Softer metals like aluminum offer easier machining with acceptable tolerances at lower costs, while exotic alloys, although more expensive, deliver superior performance for critical applications.
Frequently Asked Questions
Q: What makes precision machining essential for producing high-quality metal parts?
A: Precision machining delivers parts with extremely tight tolerances and excellent surface finishes. Automated CNC processes eliminate human error and ensure repeatability, which is critical in industries like aerospace and medical devices.
Q: How do CNC milling and turning contribute to achieving high precision in metal parts?
A: They use computer-controlled movements to create accurate cuts and shapes. CNC milling removes material from multiple angles, while CNC turning shapes parts by rotating the workpiece against a fixed tool, ensuring consistent quality and dimensional accuracy.
Q: Which industries are most dependent on precision machining services?
A: Aerospace, automotive, and medical devices rely heavily on precision machining for custom-made components that meet exact tolerances and high performance standards.
Q: What information is required when requesting a quote for precision machining services?
A: Provide detailed design documents such as CAD files and technical drawings, including tolerance and surface finish requirements, material type, production volume, deadlines, and budget constraints.
Q: How do advanced CNC technologies improve the reliability of precision machining?
A: They integrate real-time monitoring, adaptive control, and high-resolution measurement systems to ensure consistent machining processes with exact tolerances and high surface finishes.
Q: Can precision machining accommodate both low-volume prototypes and high-volume production runs?
A: Yes, it is highly versatile. It handles both low-volume prototyping and high-volume production by adjusting tool paths and production parameters without compromising quality.
Q: How does material selection impact the final cost and performance of machined metal parts?
A: Material selection influences cutting speeds, tooling wear, and finishing processes. Softer materials like aluminum are less expensive to process, while harder materials like titanium or exotic alloys require specialized tools and slower speeds, increasing cost but offering enhanced durability.
Final Thoughts
Precision machining services are integral to producing superior metal parts that consistently meet stringent quality standards. By leveraging advanced CNC technologies, selecting the right materials, and maintaining tight tolerances, each component performs reliably in high-stakes applications. HLH Sheet Metal exemplifies this commitment with its advanced systems and customer-centric approach, making it a trusted partner across diverse industries. Embrace these high-precision services to elevate your product quality and drive innovation in your field.
Get A Free Quote For Your Precision Machining Services
Talk to our experts. Our qualified engineers are always happy to answer your questions.