Table Of Contents:
- Understanding Pricing: Essential Factors in Custom Metal Parts Manufacturing Services
- Introduction
- What Are the Main Cost Drivers in Precision Metal Parts Manufacturing?
- How Does Material Selection Influence Pricing in Custom Metal Parts Manufacturing?
- What Are the Cost Components Specific to CNC Machining Services?
- How Do Different Manufacturing Processes Compare in Pricing?
- How Do Industry-Specific Requirements Affect Precision Metal Part Pricing?
- How Can Design for Manufacturability (DFM) Optimize Costs in Precision Metal Parts?
- What Quality Control Measures Influence Pricing in Precision Metal Parts Manufacturing?
- Table: Comparison of Key Manufacturing Cost Drivers
- Frequently Asked Questions
- Final Thoughts
Understanding Pricing: Essential Factors in Custom Metal Parts Manufacturing Services
Introduction
In custom metal parts manufacturing, pricing is influenced by several key factors that affect overall production costs. As an engineer, product designer, or procurement manager, understanding these cost drivers is crucial for making informed decisions about custom metal components. This article explains how material selection, labor, tooling, design complexity, and order volume impact pricing. It also covers areas such as CNC machining, various manufacturing processes, and industry-specific pricing factors in sectors like aerospace, medical devices, and automotive. Additionally, it outlines how design for manufacturability (DFM) and quality control measures can optimize costs while ensuring high performance and efficiency. This comprehensive overview will help you evaluate quotes, negotiate pricing, and collaborate effectively with manufacturing partners.
What Are the Main Cost Drivers in Precision Metal Parts Manufacturing?
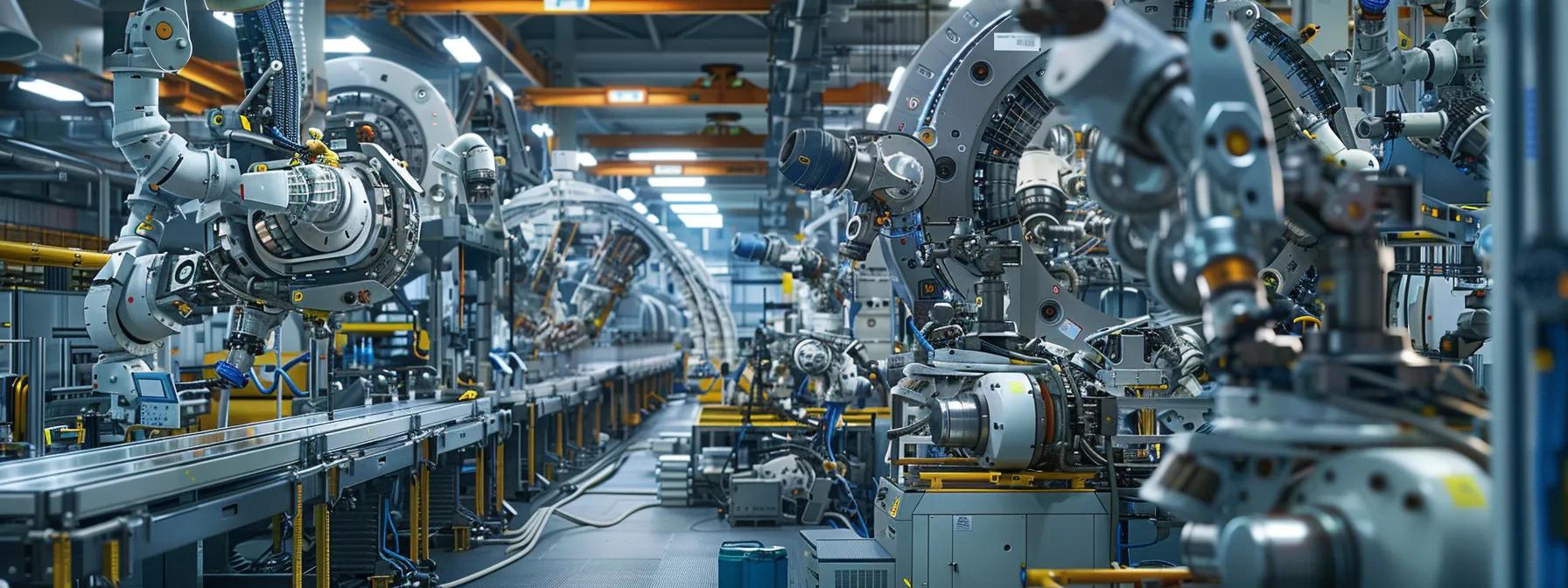
Custom metal parts pricing is primarily driven by material selection, labor, tooling and setup fees, design complexity, and order volume. Each factor plays a distinct role in determining the final cost.
How Do Material Costs Affect Custom Metal Part Pricing?
Material costs are a major component of overall pricing. The type of metal—such as carbon steel, stainless steel, aluminum, or titanium—determines both raw material expense and part performance. For instance, aerospace components often use high-grade titanium or specialty alloys, which are more expensive. Material costs also depend on market demand, metal purity, and global commodity price fluctuations. Additionally, characteristics like density and machinability affect waste during processing, influencing cost efficiency. Manufacturers monitor these factors closely to offer competitive prices.
What Role Do Labor Costs Play in Manufacturing Pricing?
Labor costs include wages, training, and benefits for skilled machinists, engineers, and quality inspectors. Precision work requires advanced technical expertise and strict adherence to safety and quality standards, which can drive labor expenses up. The complexity of processes such as CNC machining, welding, and finishing means that more labor-intensive work increases costs. Regional wage levels, productivity differences, and automation also impact these expenses. Efficient labor management reduces downtime and increases throughput, thereby helping control overall pricing.
How Do Tooling and Setup Fees Influence Total Costs?
Tooling and setup fees cover the costs associated with preparing manufacturing equipment, including custom jigs, fixtures, and molds. These fees represent a significant initial investment that is amortized over production volumes. For example, creating a high-precision mold for die casting involves considerable expense and maintenance. In low-volume production or prototype runs, these fees translate into higher per-unit costs. Balancing the initial tooling investment with expected production volume is critical for efficient cost planning.
Why Does Design Complexity Impact Manufacturing Prices?
The complexity of a part’s design has a direct effect on manufacturing costs. More intricate geometries require advanced machining processes, additional programming, and extra quality controls, which increase production time and the likelihood of errors. Complex designs may involve tighter tolerances, multiple setups, and specialized tools, all contributing to higher costs. Simplifying design elements and tolerances where possible can reduce machining time and rework, lowering expenses without compromising functionality. Integrating DFM in the planning stage is key to minimizing cost increases due to complexity.
How Does Order Volume Affect Pricing in Custom Metal Parts?
Production volume plays a crucial role in pricing through economies of scale. High production volumes allow fixed costs like tooling and setup fees to be distributed over many units, reducing the per-part cost. Conversely, low-volume or prototype orders face higher per-unit costs, since fixed costs are allocated over fewer pieces. Understanding your project’s scalability and demand is essential for planning production runs that minimize costs while meeting quality requirements.
Do you need help to calculate custom metal parts cost?
Talk to our experts. Our qualified engineers are always happy to answer your questions.
How Does Material Selection Influence Pricing in Custom Metal Parts Manufacturing?
Material selection not only determines raw material costs but also affects processing methods and overall cost structures. Comparing different materials helps in making an informed choice based on application needs.
What Are the Cost Differences Between Aluminum and Steel Parts?
Aluminum and steel offer different cost advantages. Aluminum is lighter, typically less expensive, and has good corrosion resistance, making it easier to machine and finish. Steel, however, may require additional processing like heat treatment to achieve necessary strength, making it more costly. The choice between these materials depends on performance requirements and production timelines. Selecting the right material can optimize both cost and efficiency.
How Do Material Properties Affect Manufacturing Expenses?
Key properties such as hardness, thermal conductivity, and ductility influence the manufacturing process. Harder materials demand more durable tools and slower machining speeds, increasing labor and tooling expenses. In contrast, materials with higher ductility are easier to form but require careful control during machining to maintain accuracy. Specialized alloys used in critical applications like aerospace and medical devices require tighter tolerances and thorough quality checks, further impacting cost. Evaluating both initial costs and long-term performance is essential.
How Do Market Fluctuations in Metal Prices Impact Part Costs?
Global market dynamics, including supply disruptions, political instability, and demand changes, can lead to fluctuating metal prices. Metals such as copper, stainless steel, and titanium are particularly affected by these changes. When prices increase, manufacturers pass the additional costs along the production chain. Effective forecasting and flexible procurement strategies help mitigate these fluctuations and keep projects within budget.
What Are the Cost Components Specific to CNC Machining Services?
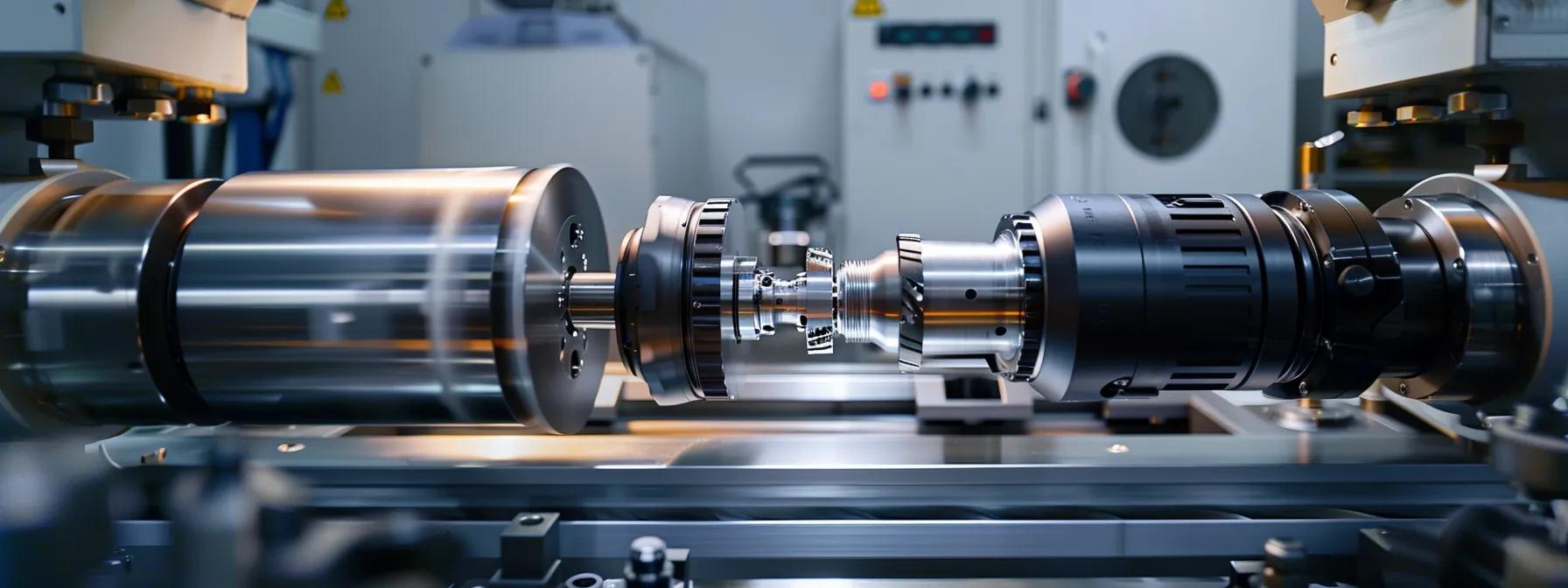
CNC machining is a precise manufacturing technique with its own cost components. Major factors include machine time, tooling, setup fees, and the complexity of the parts being produced.
How Does Machine Time Affect CNC Machining Costs?
Machine time is directly tied to production expenses in CNC machining, with costs calculated based on the active cutting, milling, or drilling time. The production of complex or high-precision parts that require multiple passes or tool changes increases machine time and expense. Strategies such as advanced programming and optimized tool paths can help shorten machine time while maintaining quality.
What Are the Tooling and Setup Costs in CNC Machining?
Tooling and setup costs involve preparing machines, calibrating equipment, and installing specific cutting tools for each part geometry. High-quality tools like carbide and high-speed steel incur higher costs and may need frequent replacement. Although initial setup costs are fixed, they are spread over the production run, so inefficiencies here can significantly affect unit costs. Implementing DFM approaches can help reduce these expenses over time.
How Does Part Complexity Influence CNC Machining Pricing?
The intricacy of part design affects CNC machining costs by increasing machine time, requiring additional tooling changes, and necessitating extra quality inspections. Features such as undercuts or deep cavities complicate the machining process and elevate risk, all of which drive up the overall cost. Simplifying designs through DFM can help manage these complexities and reduce expenses.
How Can Design for Manufacturability (DFM) Reduce CNC Costs?
DFM principles focus on simplifying part designs, reducing tolerances, and selecting materials that are easier to machine—all of which help lower machine time and tooling expenses. By streamlining production steps and fostering collaboration between design and manufacturing teams, DFM practices reduce the potential for errors and rework, leading to significant cost savings. There is a detailed section for DFM in this article. Keep reading the post.
ALSO READ: Essential Do’s and Don'ts for Metal Parts Design in Manufacturing
How Do Different Manufacturing Processes Compare in Pricing?
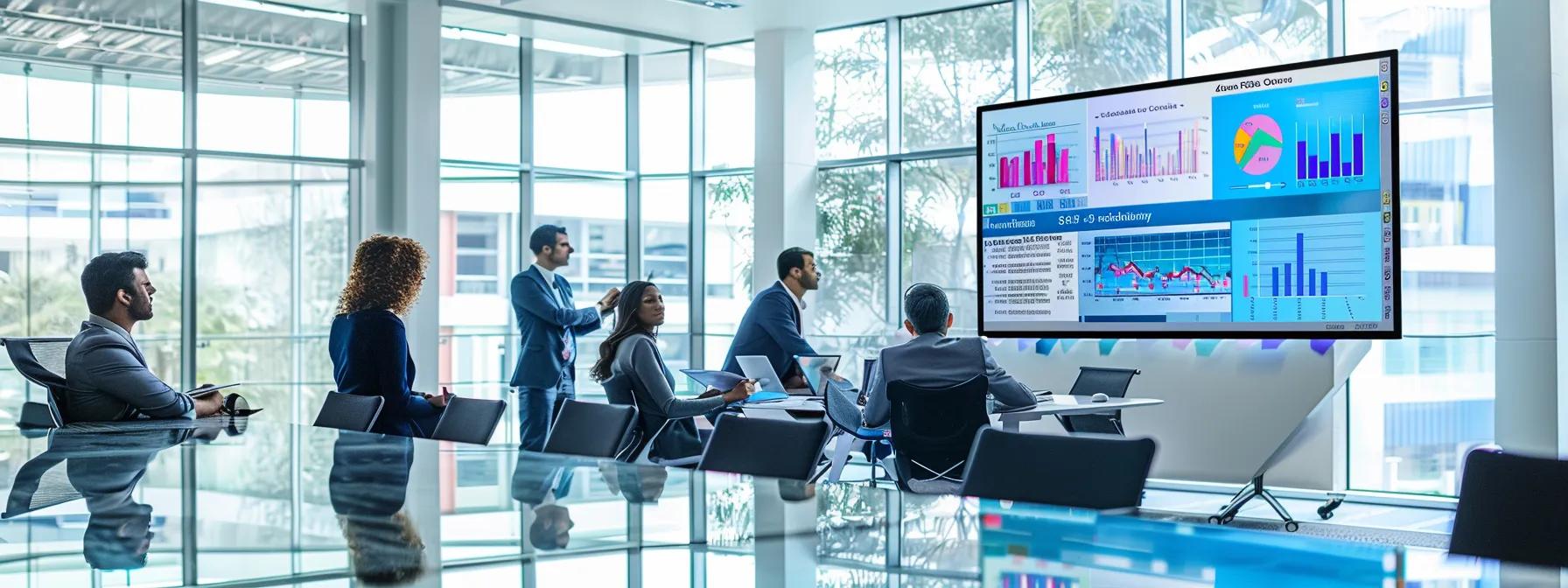
Selecting the right manufacturing process depends on understanding the cost differences between various methods such as CNC machining, stamping, and laser cutting.
What Is the Cost Difference Between CNC Machining and Stamping?
CNC machining is ideal for low-volume and custom parts due to its flexibility and high precision, though it often comes with a higher per-unit cost because of machine time and labor intensity. Stamping, on the other hand, requires a significant initial investment in tooling, but becomes more cost-effective for high-volume production through faster cycle times and lower per-part costs once the tooling expense is amortized.
How Does Laser Cutting Pricing Differ From Other Methods?
Laser cutting offers high precision and the ability to produce clean, intricate cuts with minimal waste. It provides faster production times compared to mechanical cutting methods, though it may be more expensive for thicker materials or extremely detailed work because of increased energy consumption and machine wear. The cost-effectiveness of laser cutting depends on factors such as material thickness and design complexity.
What Are the Finishing Costs and Their Impact on Final Pricing?
Finishing processes, including powder coating, plating, anodizing, and heat treating, add value by enhancing the part’s durability and appearance. However, they also increase overall costs due to additional labor, materials, and processing time. Manufacturers must evaluate finishing options during the design phase to balance improved quality against the extra expense.
How Do Industry-Specific Requirements Affect Precision Metal Part Pricing?
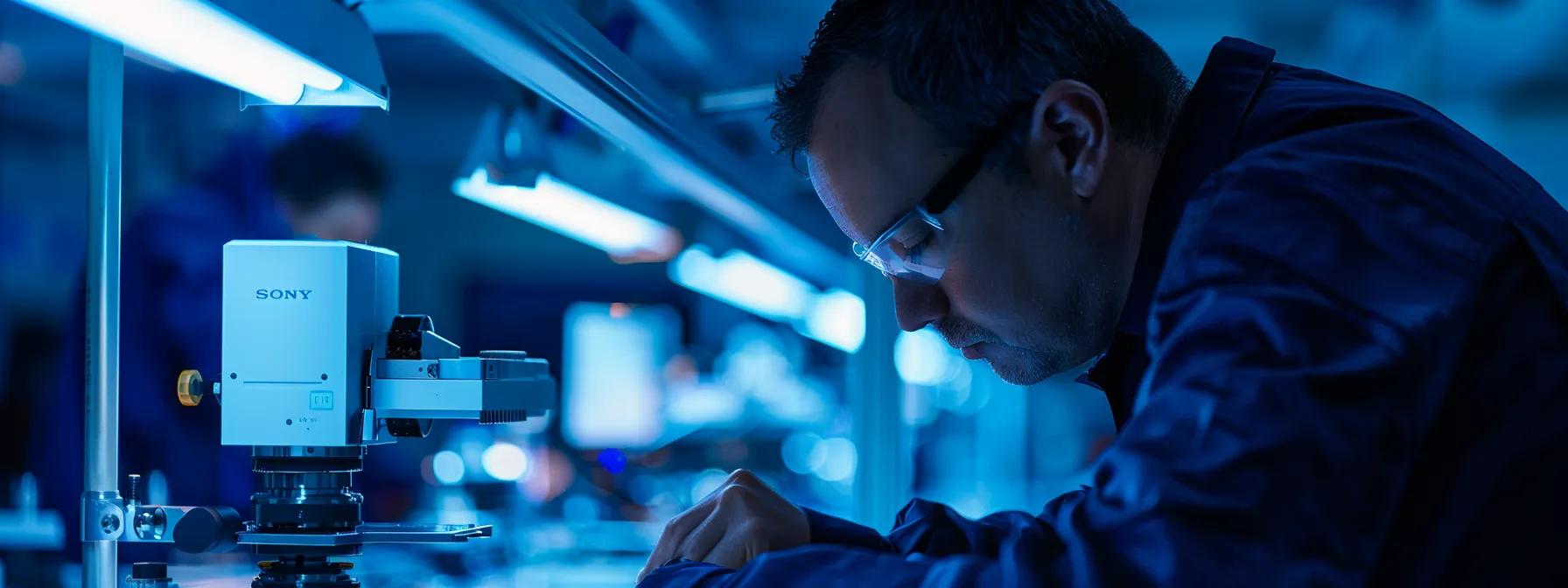
Different industries impose unique requirements that affect pricing. Sectors such as aerospace, medical devices, and automotive have distinct standards for quality, certification, and performance.
What Pricing Factors Are Unique to the Aerospace Industry?
Aerospace components must meet rigorous safety and performance standards, often necessitating the use of specialized, high-grade materials and advanced processing techniques. Additional testing, certification, and traceability requirements further increase production costs. These higher expenses are justified by the need for reliability under extreme conditions.
How Does Medical Device Manufacturing Influence Pricing?
Medical device components require high precision, biocompatibility, and strict regulatory compliance. Production often occurs in clean room environments with extensive testing and documentation, all of which drive up costs. While these measures increase expenses, they are essential to ensure patient safety and product reliability.
What Are the Pricing Considerations for Automotive Precision Parts?
Automotive components must balance durability, performance, and cost-effectiveness. High production volumes help lower costs through economies of scale, but manufacturers must also consider material selection, design complexity, and the need for advanced finishing techniques to ensure consistent quality and safety in demanding environments.
How Can Design for Manufacturability (DFM) Optimize Costs in Precision Metal Parts?
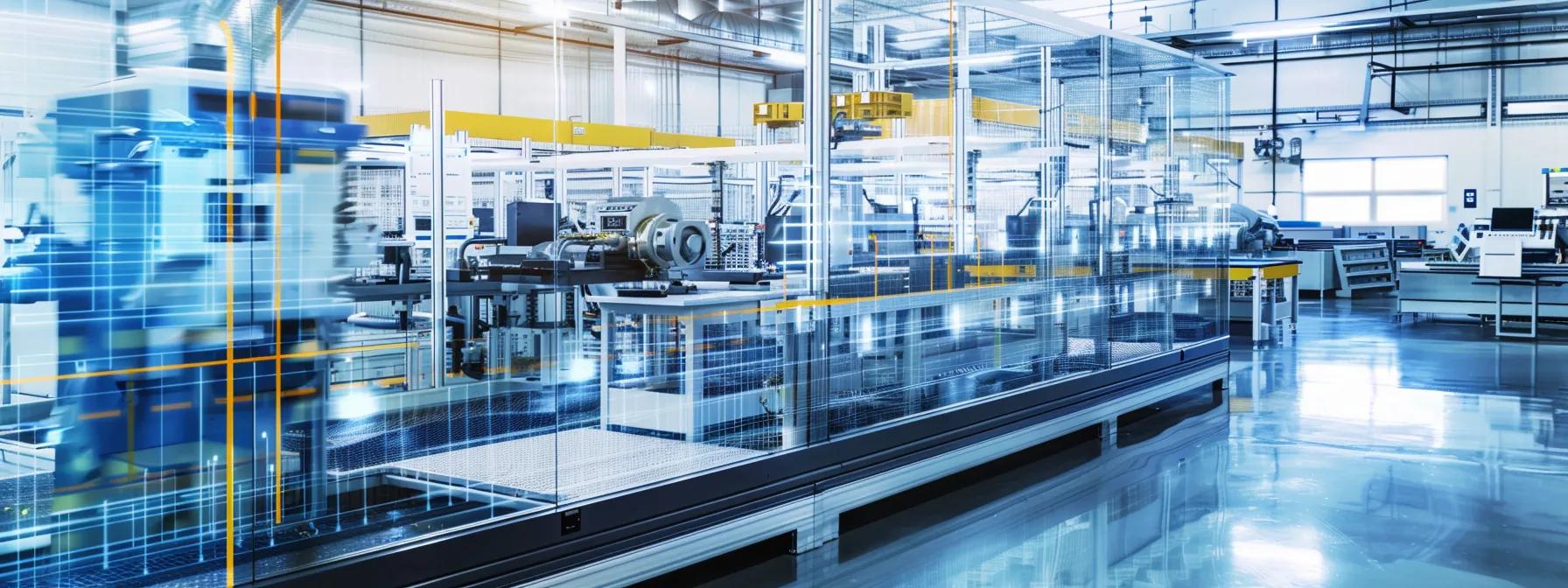
DFM is a strategic approach that simplifies part design to reduce manufacturing costs while maintaining quality. By focusing on design simplification, appropriate tolerances, and suitable material selection, DFM transforms complex components into cost-effective products.
What Are Best Practices for Cost-Effective Part Design?
Effective part design starts with simplicity. Consolidating components, standardizing sizes and shapes, and avoiding unnecessary features all help lower machining time and tooling costs. Collaboration between design engineers and production teams ensures that cost-effective strategies are integrated early in the design phase, resulting in parts that are both reliable and easier to manufacture.
How Does Reducing Tolerances Affect Manufacturing Costs?
Overly tight tolerances can lead to longer production cycles, increased scrap rates, and higher quality control expenses. Where functionality allows, relaxing tolerances reduces machining time and tool wear, thereby lowering overall production costs. Engineers should carefully balance precision with cost efficiency in their designs.
How Can Material Choice and Design Simplification Lower Expenses?
Selecting materials that are easier to machine can reduce tool wear and energy consumption. A simplified design minimizes the need for multiple setups and complex programming. By aligning material selection with streamlined design, manufacturers can lower production time and waste while maintaining high quality.
What Quality Control Measures Influence Pricing in Precision Metal Parts Manufacturing?
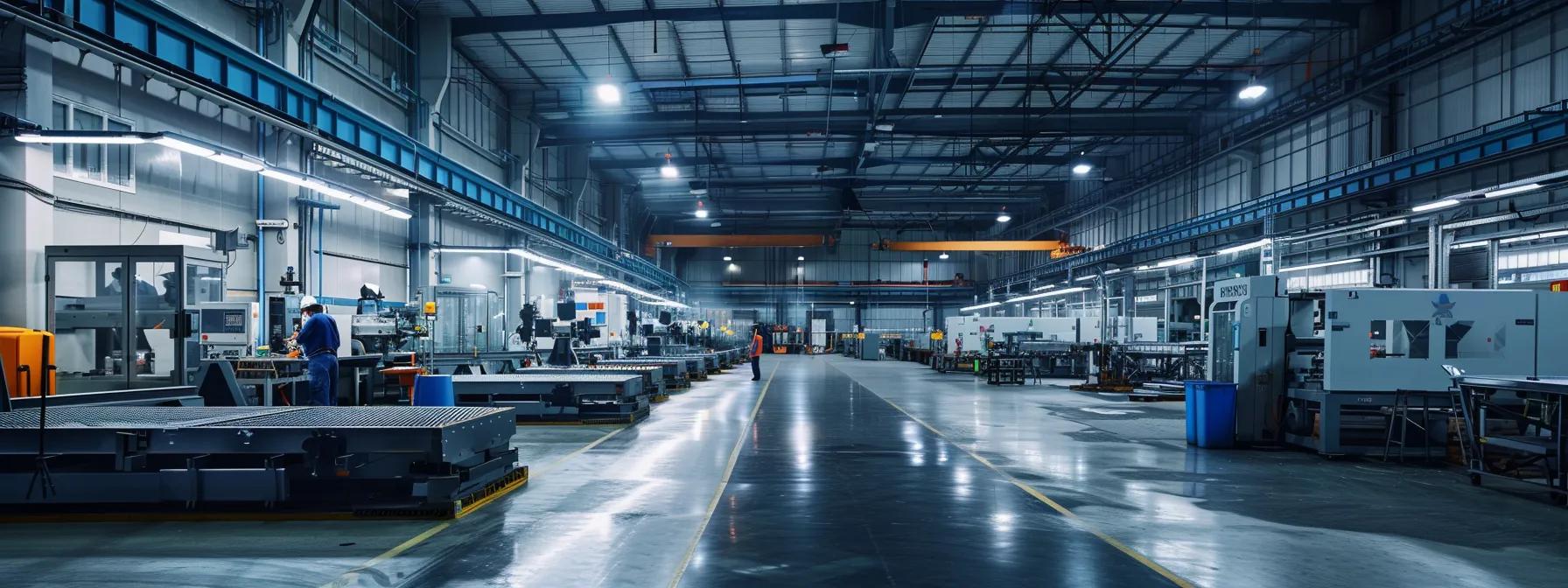
Robust quality control is essential to ensure that precision metal parts meet stringent performance standards. Although quality control adds to production costs, it minimizes defects, reduces rework, and extends product lifetime, ultimately offering better value.
How Do Inspection and Testing Procedures Affect Pricing?
Inspection and testing using technologies like coordinate measuring machines (CMM), ultrasonic testers, and laser scanners are vital to verify part accuracy. While these processes add upfront costs, they reduce the risk of defects and expensive recalls. Automated inspection can also help lower labor expenses while maintaining high quality.
Why Is Certification Important and How Does It Impact Cost?
Certification from bodies such as ISO 9001 or AS9100 ensures that manufacturing processes meet international quality standards. Although certification requires significant investment in systems, audits, and documentation, it builds trust, reduces liability, and can enhance market acceptance, which helps justify the increased cost.
How Does Quality Control Improve Value Despite Higher Costs?
Comprehensive quality control reduces failures and rework, safeguarding the manufacturer’s reputation and improving customer satisfaction. The long-term savings from fewer defects and consistent product performance offset the initial extra expense, making quality control an investment rather than just a cost.
Table: Comparison of Key Manufacturing Cost Drivers
Cost Driver | Impact on Pricing | Example/Attribute | Effect on Final Cost |
---|
Material Costs | High variability based on material type | Titanium vs. Aluminum | Direct, substantial |
Labor Costs | Skilled workforce required | CNC machinists, inspectors | Increased per-unit cost |
Tooling & Setup Fees | Initial investments spread over volume | Custom molds, jigs | High for low-volume runs |
Design Complexity | Multiple processing steps required | Intricate geometries | Higher machining time |
Order Volume | Economies of scale effect | Batch vs. prototype | Lower per-unit cost in volume |
This table provides a concise overview of how each factor influences overall manufacturing costs and highlights opportunities for cost optimization.
Frequently Asked Questions
Q: How can I reduce production costs while maintaining high quality in precision metal parts manufacturing?
A: Implement design for manufacturability (DFM) principles to simplify geometries, optimize material selection, and reduce unnecessary tolerances. This lowers production time and tooling costs while ensuring consistent product quality.
Q: What factors should I consider when selecting the material for a precision part?
A: Evaluate the material’s mechanical properties, compatibility with the operating environment, machinability, and potential for price volatility. For example, aluminum is lightweight and corrosion-resistant, while titanium offers high strength for demanding applications.
Q: How do labor and machine time contribute to the overall cost of CNC machining?
A: Both labor and machine time are direct production costs. Each minute of machining adds to the total cost, so optimized tool paths and efficient scheduling are essential to reduce these expenses.
Q: In what ways do industry-specific requirements affect pricing for precision metal parts?
A: Different sectors, such as aerospace, medical, and automotive, impose stricter quality controls, certifications, and specialized material requirements, all of which drive up manufacturing expenses.
Q: Can upgrading quality control technology help reduce overall manufacturing costs?
A: Yes, automated inspection and testing technologies can reduce inspection times and errors. Although the initial investment is high, long-term savings from fewer defects and rework can lower overall costs.
Q: How does order volume affect pricing in precision metal parts manufacturing?
A: Higher order volumes spread fixed costs such as tooling and setup fees over more units, decreasing the per-unit cost. Low-volume or prototype orders typically incur higher costs per part.
Q: What role do finishing processes play in the final pricing of a metal part?
A: Finishing processes like powder coating, plating, and heat treating enhance a part’s durability and aesthetics but also add extra labor, material, and processing costs. Balancing these benefits with their cost is crucial.
Final Thoughts
Precision metal parts manufacturing pricing is shaped by material costs, labor, tooling, design complexity, and order volume. A thorough understanding of these factors empowers you to choose the right materials and production processes for balancing quality with cost efficiency. Emphasizing DFM and robust quality control can streamline production and reduce long-term expenses, leading to improved performance and competitive pricing in the market.
Do you need help to calculate custom metal parts cost?
Talk to our experts. Our qualified engineers are always happy to answer your questions.