Table Of Contents:
- 5 Challenges in Precision Metal Fabrication and How to Overcome Them
- What Are the Key Quality Control Challenges in Precision Metal Fabrication?
- How Does Material Selection Affect Precision Metal Fabrication Outcomes?
- What Strategies Help Manage Costs in Precision Metal Fabrication?
- How Can Lead Time Challenges Be Minimized in Precision Metal Fabrication?
- What Role Does Production Planning Play in Reducing Lead Times?
- What Are the Solutions to Skilled Labor Shortages in Precision Metal Fabrication?
- How Do Industry-Specific Challenges Influence Precision Metal Fabrication?
- How Can Advanced Technologies Transform Precision Metal Fabrication Challenges?
- Frequently Asked Questions
- Final Thoughts
5 Challenges in Precision Metal Fabrication and How to Overcome Them
Precision metal fabrication is a cornerstone of modern manufacturing that demands high accuracy, tight tolerances, and robust quality control. Manufacturers face challenges in meeting customer requirements for intricate geometries and flawless finishes while controlling production costs and lead times. This article investigates five major challenges in precision metal fabrication—from quality control issues to skilled labor shortages—and discusses actionable strategies to overcome them. You will gain insight into how advanced equipment, material selection, streamlined manufacturing processes, and workforce development practices can enhance productivity and profitability. Let’s delve into the world of precision metal fabrication to empower you with insights that drive innovation and competitive advantage.
What Are the Key Quality Control Challenges in Precision Metal Fabrication?
Quality control is the backbone of precision metal fabrication. Ensuring consistency in finishing, precise dimensions, and minimal defects is critical for product longevity. Multiple inspection methods, adherence to quality standards, and advanced equipment play pivotal roles in achieving these goals.
How Do Inspection Methods Impact Quality Control?
Inspection methods are essential to catch minute discrepancies before final assembly. Both manual and automated techniques such as visual inspections, coordinate measuring machines (CMM), laser scanning, and 3D scanning are used. Combining methods—like high-resolution imaging with digital calipers—can reduce rework costs by approximately 20%. The use of statistical process control (SPC) tools further aids in predicting and mitigating defects, ensuring that quality is built into the fabrication process rather than added afterward.
What Quality Assurance Standards Ensure Precision?
Standards such as ISO 9001, AS9100, and IATF 16949 form the framework for ensuring consistent quality. Certification processes involve rigorous audits of process documentation and operational procedures, resulting in fewer errors and enhanced product integrity. Strict adherence to these standards builds customer trust, lowers defect rates, and minimizes costly recalls. In-house quality laboratories and supplier audits further help maintain consistency and streamline the supply chain.
How Can Advanced Equipment Improve Defect Prevention?
Modern machinery like CNC machines, laser cutters, and plasma cutters offer tight control over critical dimensions and surface finishes. With tolerances as precise as 0.001 inches achieved by CNC centers, defect rates are significantly reduced. Advanced equipment integrated with real-time monitoring, machine vision, and robotics not only minimizes human error but also speeds up production. The following table summarizes the key benefits:
Equipment Type | Key Feature | Defect Reduction Benefit | Tolerance Level |
---|
CNC Machining Centers | Automated tool control | 90% reduction in dimensional errors | 0.001 inches |
Laser Cutting Systems | High precision cutting | 85% reduction in edge anomalies | ±0.5 mm |
Plasma Cutting Units | Rapid material removal | 80% reduction in thermal distortion | ±1.0 mm |
Robotic Welding Arms | Consistent welding speed | 95% reduction in weld inconsistencies | Uniform bead profile |
3D Laser Scanners | Non-contact measurement | 88% improvement in surface verification | High-resolution scanning |
By integrating such advanced tools with enterprise resource planning (ERP) systems, manufacturers can further enhance coordination between production and quality control.
Get A Free Quote For Your Precision Metal Fabrication
Talk to our experts. Our qualified engineers are always happy to answer your questions.
How Does Material Selection Affect Precision Metal Fabrication Outcomes?
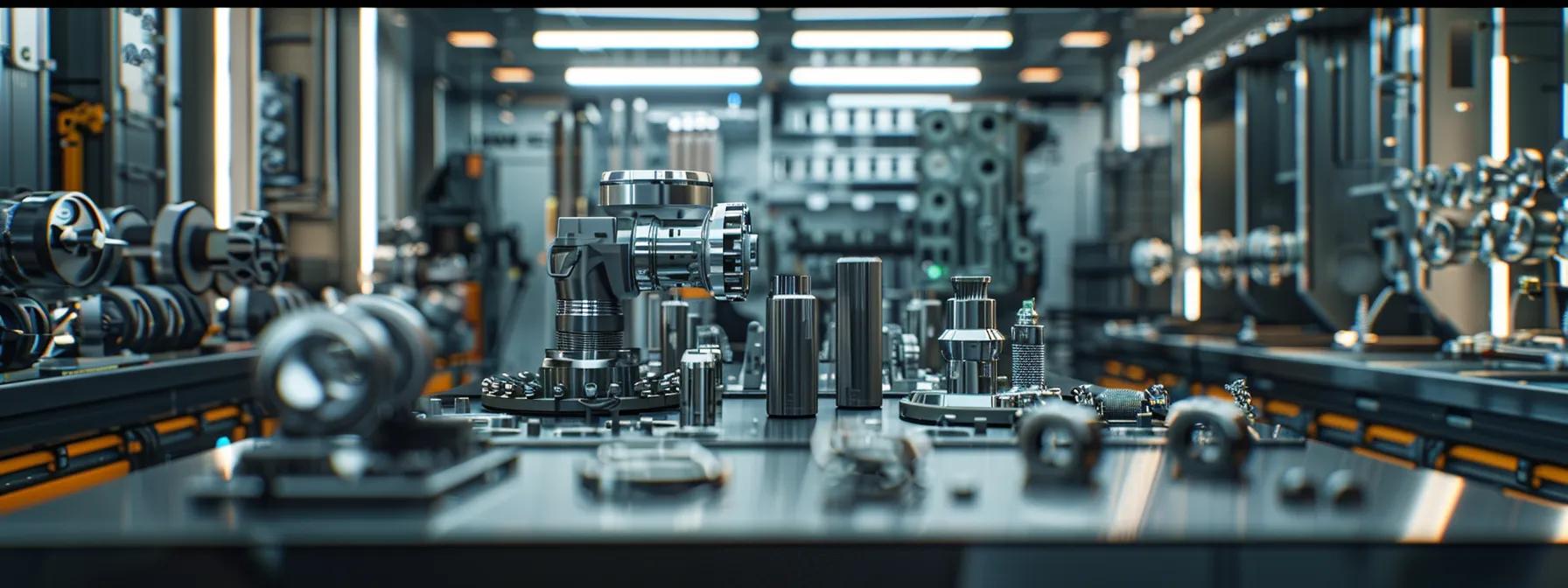
Material selection is critical for performance, durability, and cost efficiency. The choice of metal—ranging from stainless steel and carbon steel to advanced alloys like maraging steel or inconel—must be matched to design requirements and fabrication techniques.
What Are the Critical Material Properties to Consider?
Key properties include strength, ductility, thermal conductivity, and corrosion resistance. For instance, stainless steel offers excellent rust resistance and high strength, while carbon steel provides cost efficiency and ductility. Variations in alloy composition can significantly affect performance; therefore, properties such as hardness, yield strength, and tensile strength are carefully evaluated through testing methods like tensile testing and hardness measurements.
How Can Supply Chain Management Improve Material Sourcing?
Effective supply chain management ensures high-quality materials are delivered on time. Practices such as strict supplier qualification, regular audits, digital tracking of raw material batches, and long-term contracts help reduce variability in material quality. Additionally, implementing quality checks like chemical composition analysis at the receiving stage minimizes risks associated with material degradation, thereby optimizing overall production outcomes.
Why Is Collaboration With Experienced Engineers Essential?
Working with experienced engineers provides specialized expertise in metallurgy and fabrication. Their insights help to match material properties with design requirements, mitigate risks such as unexpected material behavior, and suggest innovative alloy compositions. Such cross-functional collaboration accelerates product development and ensures that every component is manufactured with the best-suited material, enhancing overall reliability.
What Strategies Help Manage Costs in Precision Metal Fabrication?
Cost management involves balancing high-quality outputs with competitive pricing. Effective strategies include optimizing manufacturing processes, applying value engineering, and negotiating with suppliers.
How Can Manufacturing Processes Be Optimized for Cost Reduction?
Streamlining production through lean manufacturing techniques—like just-in-time inventory and continuous improvement (Kaizen)—enhances productivity and reduces waste. Automation helps reduce labor costs and minimizes errors. Integration of computer-aided design (CAD) with computer-aided manufacturing (CAM) ensures a seamless transition from design to production, thereby cutting delays. Data-driven decision making and advanced process control further reduce setup and cycle times, contributing to substantial cost savings, sometimes up to a 25% reduction.
What Is Value Engineering and How Does It Reduce Expenses?
Value engineering examines every element of the fabrication process to identify cost-saving opportunities without sacrificing quality. This method involves cross-functional teams that analyze material usage and design efficiency. For example, replacing a high-cost alloy with a less expensive alternative that meets performance needs can significantly lower production costs. Additionally, value engineering can lead to simpler manufacturing processes and lower maintenance expenses.
How Do Supplier Negotiations Impact Cost Management?
Effective supplier negotiations secure competitive pricing and ensure reliable quality. Strategies include long-term relationships, bulk purchase agreements, and leveraging competitive bids. Digital procurement systems help track supplier performance and market trends, enabling renegotiation of terms as needed. Clearly defined service level agreements (SLAs) further ensure that suppliers meet quality and delivery standards, creating a win-win scenario for both parties.
How Can Lead Time Challenges Be Minimized in Precision Metal Fabrication?
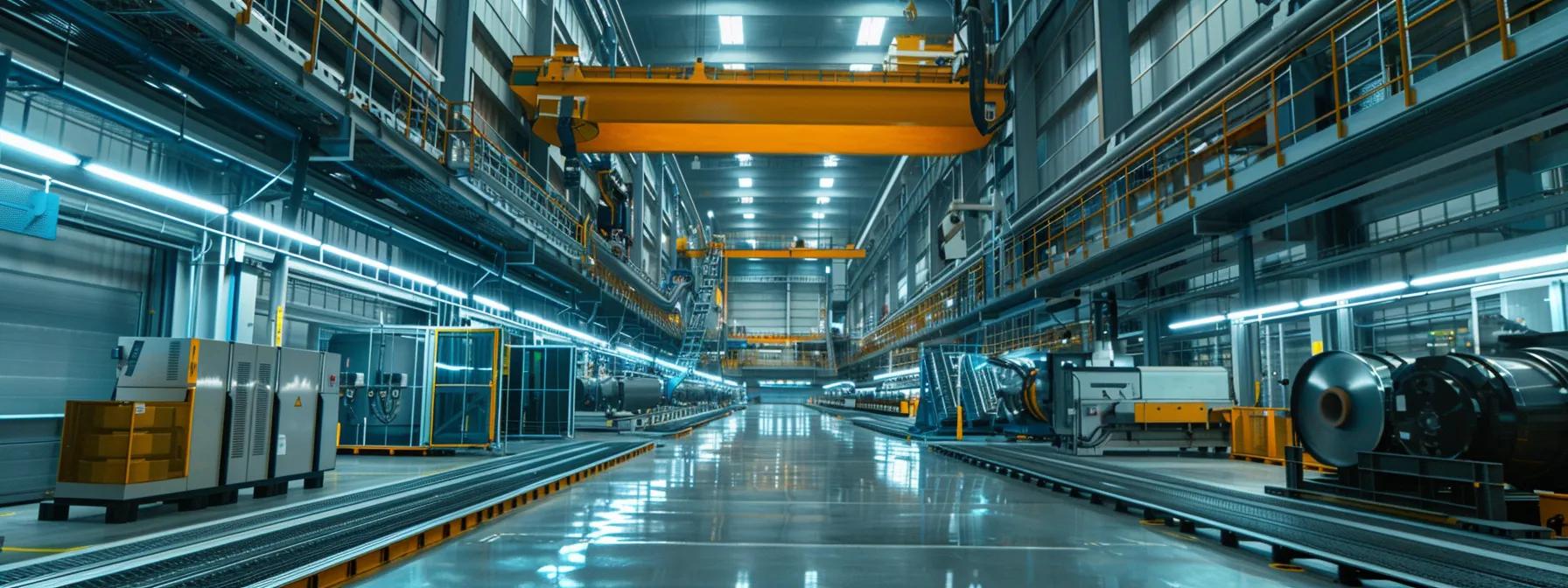
Reducing lead times is essential for staying competitive and meeting customer deadlines. Key strategies involve effective production planning, lean manufacturing, and the use of advanced equipment.
What Role Does Production Planning Play in Reducing Lead Times?
Meticulous production planning synchronizes all stages—from material procurement to final inspection—helping to avoid bottlenecks. Techniques such as the Critical Path Method (CPM) and Material Requirements Planning (MRP) ensure efficient scheduling, while robust interdepartmental communication helps quickly address delays. Contingency plans, like reserving extra machine time or maintaining buffer stocks, also play a crucial role in keeping production on schedule.
A summary of production planning strategies is as follows:
Strategy | Benefit | Impact on Lead Time | Example |
---|
Critical Path Method | Identifies essential tasks | Reduces delays | Scheduling crucial machining |
Material Requirements Planning | Optimizes inventory levels | Prevents shortages | Just-in-time ordering |
Real-Time Monitoring | Immediate issue detection | Minimizes downtime | Automated sensor integration |
Contingency Planning | Prepares for unexpected delays | Maintains schedule | Reserving backup machine time |
Cross-Departmental Communication | Accelerates problem-solving | Streamlines operations | Regular status meetings |
How Do Lean Manufacturing Principles Improve Efficiency?
Lean practices eliminate waste and streamline production. Techniques such as 5S, Kaizen, and value stream mapping reduce idle time and enhance workflow. By standardizing setup procedures and utilizing quick-change tooling, manufacturers can significantly reduce cycle times and lower production costs.
How Does Advanced Equipment Shorten Production Cycles?
Modern equipment such as CNC machines, laser cutters, and robotic arms allow for continuous, high-speed production with minimal error rates. Interconnected digital systems ensure that production stages are synchronized, while predictive maintenance features reduce unplanned downtime. This results in a smoother production cycle, enabling manufacturers to meet tight deadlines without sacrificing quality.
What Are the Solutions to Skilled Labor Shortages in Precision Metal Fabrication?
A shortage of skilled technicians and engineers can compromise both quality and efficiency. Addressing this challenge involves training, automation, and fostering a positive work environment.
How Do Training and Development Programs Enhance Workforce Skills?
Comprehensive training programs provide employees with up-to-date knowledge on advanced machinery and quality control techniques. Hands-on training, simulation modules, and certification programs improve productivity and reduce errors. Mentoring and apprenticeship models further help transfer specialized skills, resulting in enhanced operational efficiency and lower turnover rates.
What Is the Impact of Automation on Skilled Labor Needs?
Automation reduces reliance on manual labor by handling repetitive tasks with high accuracy. This frees skilled workers to focus on complex, value-added tasks like design optimization and problem-solving. Advanced robotics and user-friendly automated systems not only improve throughput but also help bridge the labor gap by requiring minimal supervision and training.
How Can a Positive Work Environment Retain Skilled Employees?
A positive work environment that values collaboration, continuous learning, and open communication is key to retaining skilled employees. Competitive compensation, clear career progression, flexible work schedules, and recognition programs promote high morale and lower turnover. Such a culture ensures that employees remain motivated and loyal, further strengthening the overall workforce.
How Do Industry-Specific Challenges Influence Precision Metal Fabrication?
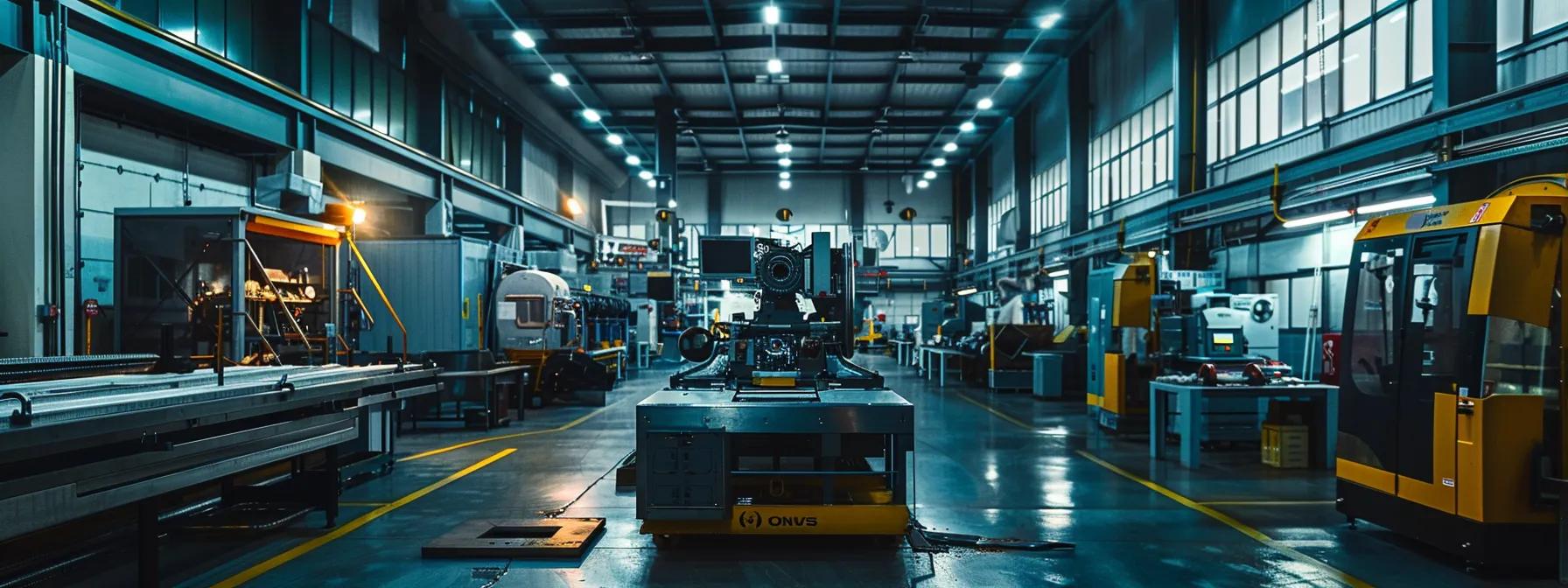
Different industries impose unique challenges on precision metal fabrication. Sectors such as aerospace, medical devices, and electronics each demand distinct quality, material, and cost considerations.
What Unique Quality Requirements Exist in Aerospace Fabrication?
Aerospace fabrication requires the utmost precision, reliability, and safety. Components must meet strict certifications and tolerate extreme conditions such as high thermal stress and vibration. Advanced inspection methods and rigorous quality controls—using techniques like electron microscopy and non-destructive testing—are essential to ensure that every part meets these high standards. Specialty materials like titanium alloys also require specific machining processes and surface treatments.
How Are Medical Device Fabrication Challenges Addressed?
Medical device fabrication is governed by stringent FDA and ISO 13485 standards. In addition to dimensional accuracy, components must pass biocompatibility and chemical stability tests. Cleanroom manufacturing and advanced automation minimize contamination risks, while traceability systems ensure full regulatory compliance. These measures not only guarantee patient safety but also control production costs.
What Are the Electronics Industry’s Material and Cost Considerations?
In the electronics sector, components such as heatsinks, connectors, and enclosures are fabricated to offer excellent thermal conductivity and EMI shielding. Manufacturers must balance tight tolerances with cost efficiency, often using materials like aluminum and copper. Advanced surface treatments enhance durability and performance, making rigorous supplier negotiations and testing critical to meet both performance and budgetary targets.
How Can Advanced Technologies Transform Precision Metal Fabrication Challenges?
Advanced technologies are reshaping precision metal fabrication by enhancing efficiency, accuracy, and consistency. Modern manufacturing tools help address challenges related to lead time, quality control, and labor shortages.
What Are the Benefits of CNC Machining and Laser Cutting?
CNC machining and laser cutting enable high accuracy and repeatability. Automated tool paths ensure that large production runs maintain tolerances as tight as 0.001 inches, significantly cutting down human error and material waste. Laser cutting, with its non-contact process, guarantees clean, precise cuts for complex geometries. This combination results in shortened production cycles and increased throughput.
How Does Automation Improve Lead Time and Labor Challenges?
Automation systems—such as robotic arms and automated inspection devices—run continuously with minimal supervision, reducing cycle times significantly. By handling repetitive tasks, these systems allow skilled employees to concentrate on critical decision-making and troubleshooting. Integration with ERP systems enables proactive scheduling and inventory management, further enhancing operational resilience and reducing lead times.
How Can Data-Driven Quality Control Enhance Fabrication Accuracy?
Data-driven quality control uses real-time monitoring and advanced analytics to continuously assess machine performance and process variables. Statistical process control (SPC) techniques help identify trends that may indicate emerging quality issues, allowing for prompt corrective actions. This approach not only reduces scrap rates and rework costs but also fosters continual improvements and compliance with industry standards.
Frequently Asked Questions
Q: What is precision metal fabrication?
A: It is the process of crafting metal components with extremely tight tolerances and high accuracy through advanced techniques such as CNC machining, laser cutting, and automated assembly. This process is vital in industries like aerospace, medical devices, and electronics.
Q: How do advanced technologies impact fabrication efficiency?
A: Technologies like CNC machining, laser cutting, and automation reduce cycle times, minimize human error, lower scrap rates, and enable consistent high-volume production, significantly improving overall efficiency.
Q: Why is quality control challenging in metal fabrication?
A: Detecting minute deviations in dimensions, surface finishes, and material properties requires multiple specialized inspection methods and strict adherence to quality standards, making quality control a complex but essential aspect of fabrication.
Q: How can lean manufacturing principles reduce production costs?
A: Lean principles eliminate waste and streamline processes through just-in-time inventory, continuous improvement, and standardized procedures, leading to reduced overhead, shorter lead times, and overall cost savings.
Q: What role does material selection play in fabrication outcomes?
A: The right material choice affects a component’s strength, durability, thermal conductivity, and overall cost-effectiveness. Selecting appropriate materials ensures that components meet design requirements and perform reliably.
Q: How do training programs mitigate skilled labor shortages?
A: Comprehensive training enhances workforce skills, reduces errors, and improves productivity. Mentoring and continuous learning ensure that skilled workers are retained and equipped to use advanced technologies effectively.
Q: What are the benefits of data-driven quality control?
A: It leverages real-time monitoring and analytics to detect process deviations early, reduce defect rates, and support ongoing improvements and regulatory compliance.
Final Thoughts
Precision metal fabrication faces challenges from stringent quality control and cost management to reducing lead times and addressing skilled labor shortages. By utilizing advanced inspection methods, optimized production planning, and modern automation technologies, manufacturers can enhance product quality while controlling costs. Collaboration with experienced engineers and robust supplier networks further solidify operations, transforming obstacles into opportunities for innovation and long-term success in manufacturing.
Get A Free Quote For Your Precision Metal Fabrication
Talk to our experts. Our qualified engineers are always happy to answer your questions.